The business world as we know it today is highly competitive, always striving to find new methods to attract clients and follow market trends.
The main goal is to provide clients with impeccable service in the blink of an eye. This is most obvious in the retail industry.
To achieve their goal, businesses turn to lean management and are more heedful of their inventory management. Their inventory control must be spot on, neither being wasteful with their stock nor a wasteland without any.
In this article, we will explain in detail what inventory management is, what techniques it uses, and its types.

In this article:
What is inventory management?
Inventory management is the strategy used to control inventory flow — from purchasing, stocking, and organizing to using and selling.
Good inventory management recognizes market trends and ensures that orders are fulfilled and shortages prevented. It improves the business’ internal organization, as well as its customer relations.
Customer satisfaction is especially crucial in the retail business. This is because this industry aims to meet customer demands all the time while minimizing stock shortages and overstock.
Efficient retail inventory management considers the following aspects:
- What products sell best and in what locations,
- What the optimal number of items per store is,
- When to order a new supply of goods,
- What items are best sold online and in stores,
- How to reduce costs of transportation and warehouses, and
- How to plan a discount scheme.
5 Stages of inventory management
The inventory management process has 5 stages, and each requires strict control and organization. These stages are:
- Purchasing — the purchase of raw materials that will be used in the production or purchase of finished goods ready for sale or shipment,
- Production — the process of making products out of said materials,
- Inventory holding — storing raw materials, components, or finished products and checking their quality until they are sold,
- Sales — selling products and receiving payment, and
- Reporting — documenting what was sold and how much was earned.
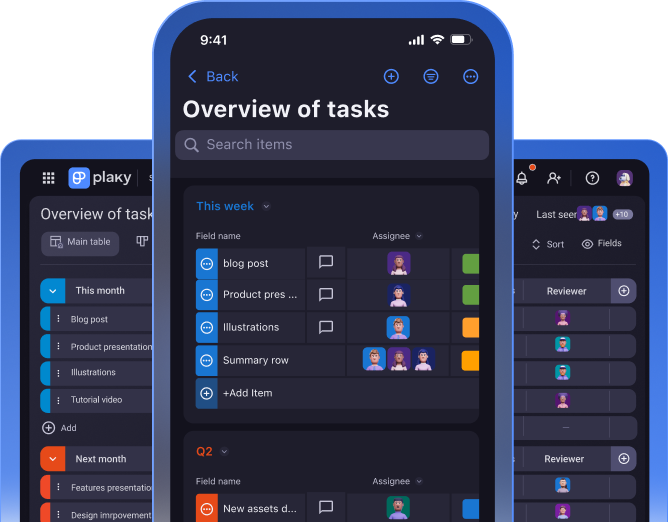
Benefits of inventory management
We spoke to Robert Khachatryan, CEO of Freight Right Global Logistics, about the benefits of managing inventories, and he immediately pointed out its impact on customer satisfaction:
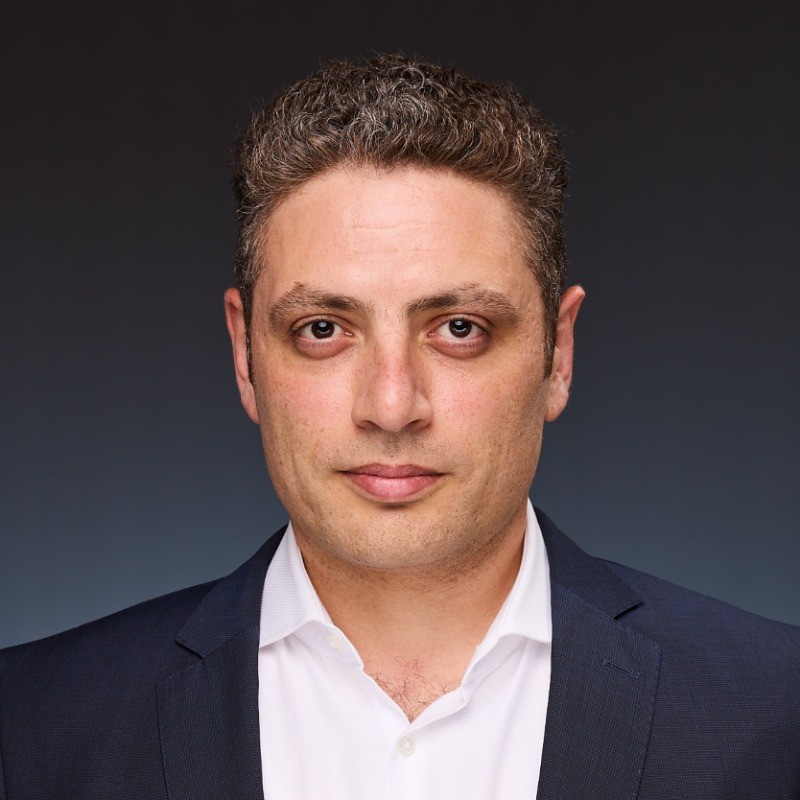
Robert Khachatyan
CEO of Freight Right Global Logistics
“By maintaining optimal stock levels, we ensured timely order fulfillment, resulting in a significant increase in customer satisfaction scores.”
When your inventory management is effective, customers don’t have to wait long to get their orders, so their buying experience is improved.
There’s another, more immediate benefit Robert pointed out:
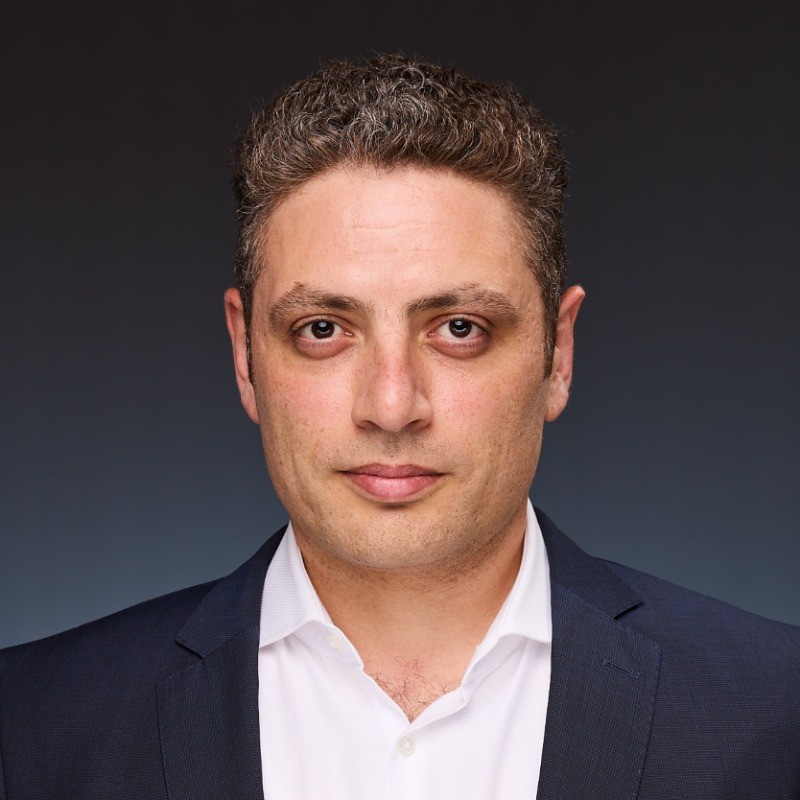
Robert Khachatyan
CEO of Freight Right Global Logistics
“Effective inventory management led us to significant cost savings, particularly in warehousing and spoilage costs, improving the bottom line.”
So good inventory management can have a positive impact on your budget.
However, there are even more benefits to inventory management, some of which are:
- Detailed insight into the amount of available stock — it allows you to order the amount you need.
- Better planning — it helps you avoid stockouts and excess stock.
- Understanding of trends and demand — it enables inventory turnover and higher profits.
- Better warehouse organization and supervision — it allows faster item location.
- Improved cash flow — money that’s poured into the supply returns in sales, and improving inventory creates a better flow.
Challenges of inventory management
Inventory management does come with its own difficulties, the most common among them — according to Robert — being supply chain disruptions:
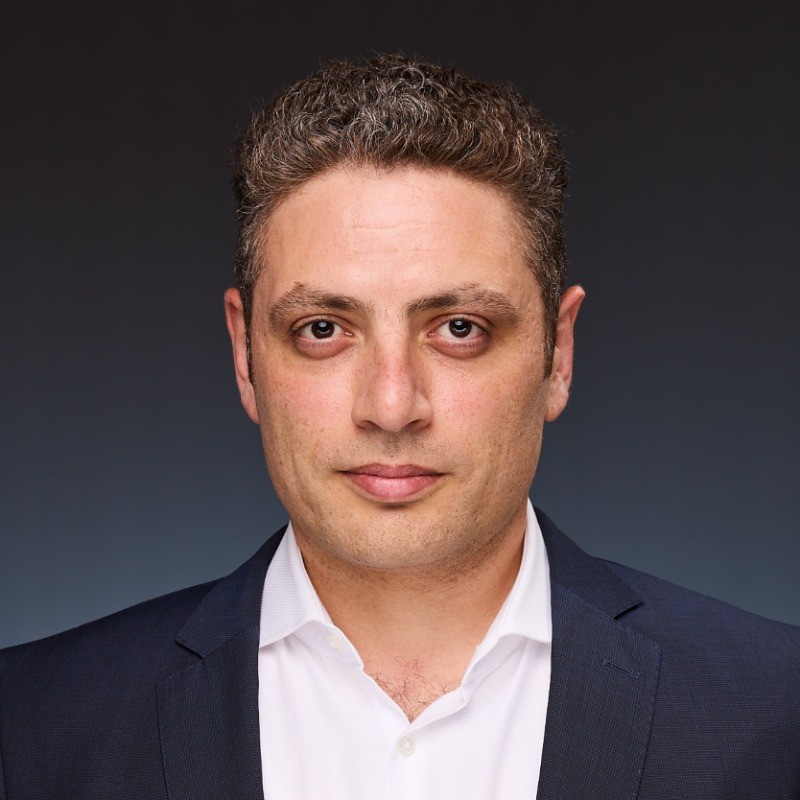
Robert Khachatyan
CEO of Freight Right Global Logistics
“We faced challenges with unexpected supply chain disruptions, leading to stockouts of critical items. We required agile responses and diversified supplier networks to mitigate impact.”
If your supply chain management is poor, you won’t be aware of the changes in supply chains, and your inventory will suffer. In a critical situation such as the one Robert pointed out, it can make all the difference.
Robert also warned us about the other side of the coin, where customer demand changes can affect your business:
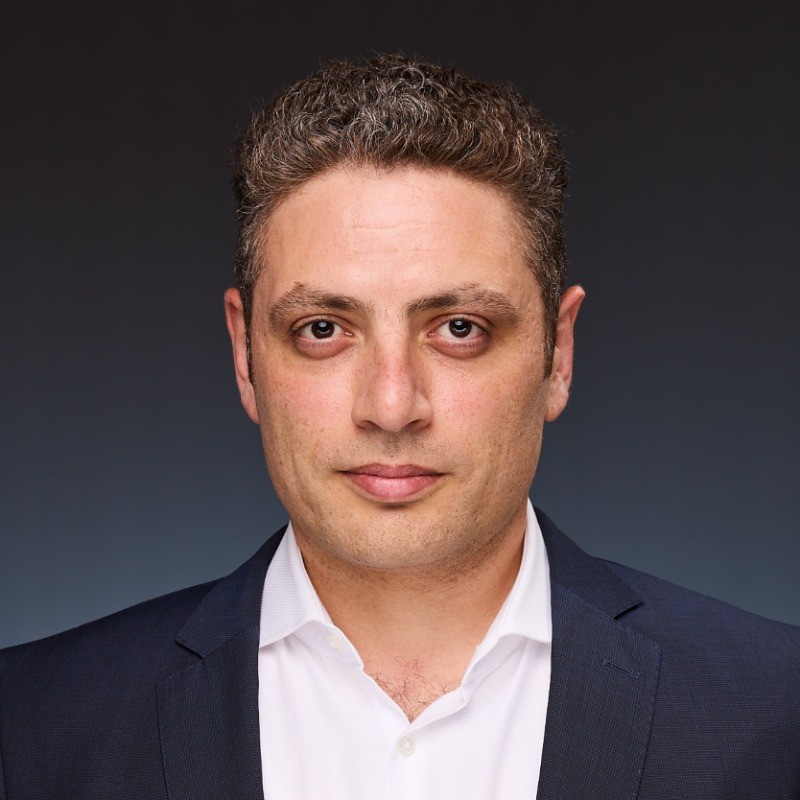
Robert Khachatyan
CEO of Freight Right Global Logistics
“We experienced difficulties in forecasting demand for new products, leading to either excess inventory or stock shortages.”
This challenge calls for a constant understanding of trends. Being able to keep up with and predict the market shifts is key.
Some other common challenges of inventory management are:
- Getting precise data on available inventory — having this enables you to avoid stock-outs and overstocks.
- Warehouse management — allows similar items grouping and better coordination.
- Poor procedural strategy — if the system for documenting inventory is outdated, it can lead to mistakes and cause delays.
13 Inventory management techniques
Any business that involves inventory management chooses the techniques of inventory control that suit it best. The techniques of stock organization used by one retailer or manufacturer might not be right for their partners or competitors.
Let’s have a look at some of these techniques.
Technique #1: ABC analysis
ABC analysis is based on the status of a particular item, i.e. its level of popularity. Items are divided into A, B, and C categories, so that:
- Category A includes items that sell best and are most popular,
- B includes less popular items, and
- C includes the least popular items.
It is estimated that category A represents 20% of the inventory, and categories B and C have an equal share of the rest.
Robert has also used this method, and claims it’s quite effective:
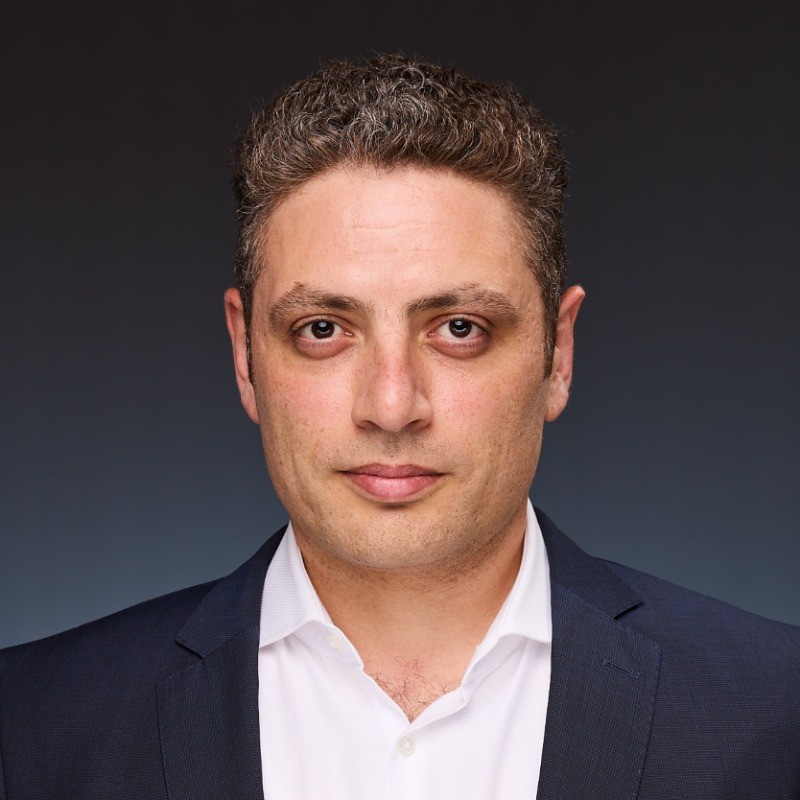
Robert Khachatyan
CEO of Freight Right Global Logistics
“We adopted ABC analysis to prioritize inventory, focusing resources on high-value items (A items). This strategy improved stock turnover rates by up to 15%, enhancing overall efficiency.”
Technique #2: Just-in-time (JIT)
Just-in-time (JIT) is the method that implies keeping low levels of stock and making new orders just in time when you need them for production.
This way, you need less storage space, efficiently spend money, and reduce waste by keeping only the inventory you need at the moment.
This technique can be used to reduce costs, as Robert’s experience tells us:
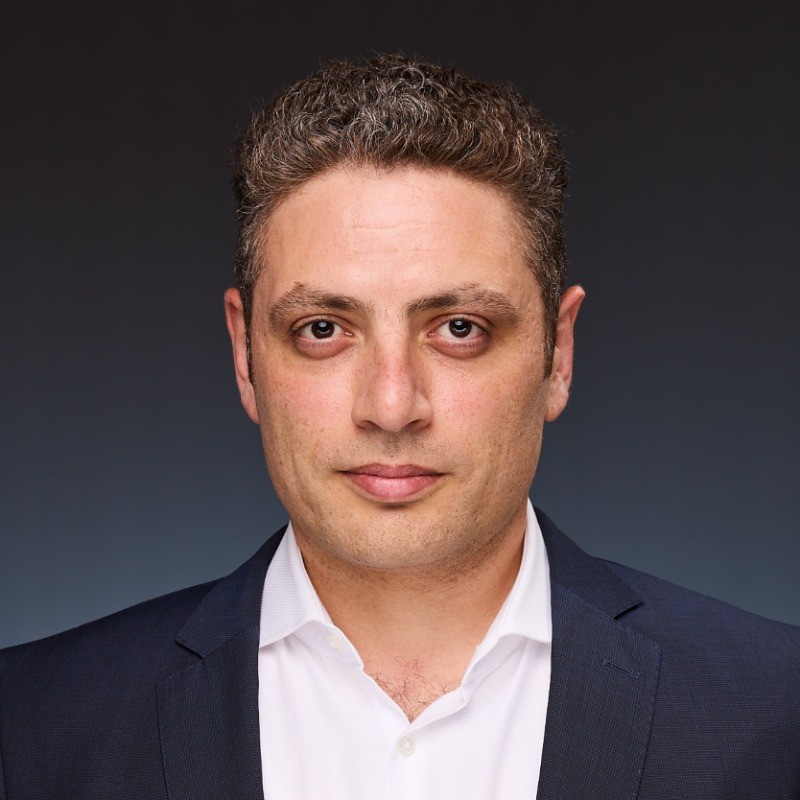
Robert Khachatyan
CEO of Freight Right Global Logistics
“We implemented JIT to reduce inventory holding costs, which led to a 25% decrease in storage expenses. This method required precise coordination with suppliers to ensure timely delivery of goods.”
Technique #3: Dropshipping
This model is usually applicable to smaller businesses, which means that ordered items are sent from warehouses, wholesalers, or bigger suppliers — directly to the customer.
A retailer represents an intermediary between the customer and the supplier.
Technique #4: Batch tracking
Batch tracking is a technique that enables the grouping of items and tracking them in matters of expiration date and defectiveness.
This technique is widely used in the food industry because many food items have expiration dates or decay rapidly.
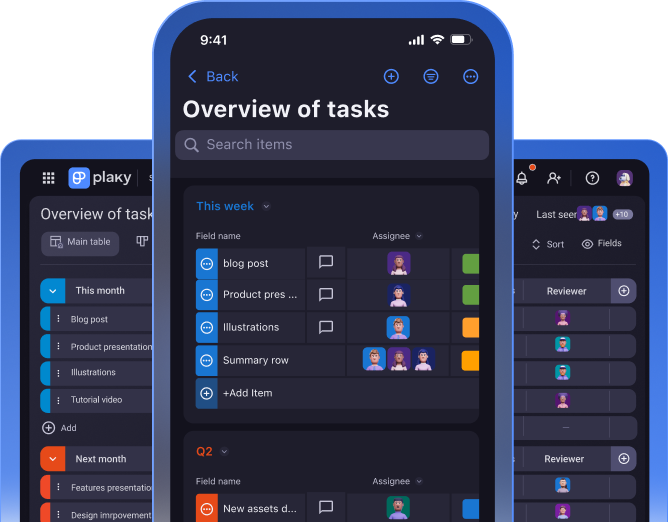
Technique #5: Bulk shipments
Bulk shipments are considered a cheap method of transporting goods as goods are directly packed into trucks or ships.
It is a great solution for managing goods with long service life.
Technique #6: Consignment
The consignment technique refers to the situation where goods are sent to a company by a wholesaler, but those goods are not paid to a wholesaler until they are sold to customers.
It is usually used with seasonal goods and those liable to rot.
Technique #7: Six Sigma
The Six Sigma method is one of the project management techniques that can also be applied to inventory management. Based on data, this method can help improve services and eliminate defects in the inventory management process.
The principles of Six Sigma are usually applied to production, product development, and many other areas.
Technique #8: Cross-docking
The cross-docking technique is used to avoid holding inventory in a warehouse for days.
When goods arrive at a warehouse, they are immediately rearranged and loaded into other trucks or ships. This minimizes transportation costs and the number of warehouse workers.
Technique #9: FIFO and LIFO
FIFO stands for first in, first out, and this method is used if you tend to sell the oldest items first. LIFO stands for last in, first out, and this method strives to sell the newest inventory first because it is the most expensive.
Both techniques are used in inventory valuation.
Technique #10: Demand forecasting
Demand forecasting or demand planning is a highly useful technique that requires analyzing past trends based on previous sales figures.
Once again, Robert confirms from experience just how effective this method is:
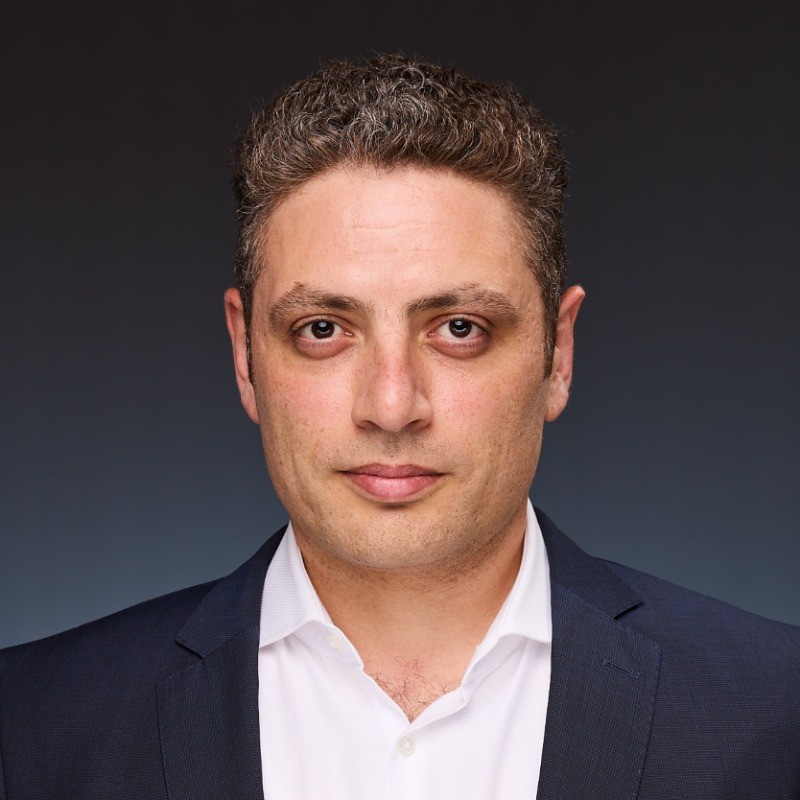
Robert Khachatyan
CEO of Freight Right Global Logistics
“We utilized advanced analytics for demand forecasting, achieving a 25% improvement in order accuracy and reducing overstock situations.”
Being able to predict demand shifts can greatly improve the accuracy of your inventory management. Generally, forecast intervals are 30 days, 3 months, and one year.
Technique #11: Economic order quantity
Economic order quantity (EOQ) is a formula that’s used to determine the optimal order quantity and thus cut costs of overhead and storage. This technique, however, assumes that demand and holding costs remain stable.
To mitigate demand changes, you can keep a safety stock on hand for emergencies.
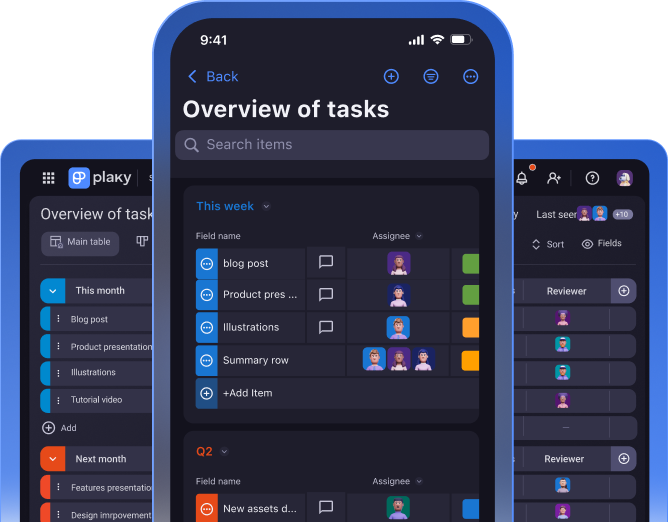
Technique #12: Backordering
Backordering represents a management method that enables customer orders even though some items are currently unavailable or will be available for the first time in the near future.
This technique is effective because sales go up and customers remain loyal.
Technique #13: Minimum order quantity
According to this model, a company orders minimum amounts of a certain product. The minimum order can have its set price or a certain number of items.
This technique is a great choice for small businesses, especially when it is used in the long run.
💡Plaky Pro Tip
If you want to improve the way you track inventory and the parameters you use, check out these inventory management templates:
2 Types of inventory management systems
It is difficult to handle raw material purchases, follow trends, respond to customer demands, and organize the distribution of goods. This is where inventory management systems come into play. They are essential for any business, and managers choose them depending on the needs and cost.
There are 2 main types of inventory management systems:
- Periodic
- Perpetual.
Type #1: Periodic inventory management system
This system is usually used by smaller businesses that don’t have loads of inventory. It involves individually counting every piece of physical inventory.
This is referred to as inventory counts — it’s based on the manual counting of items and recording on a spreadsheet or some other document. This is done at specified intervals, such as monthly, quarterly, or annually.
This system is very simple, but it isn’t the right fit for larger businesses. Also, it is error-prone, and it is advisable to do the counting more often to avoid mistakes.
Type #2: Perpetual inventory management system
This type of inventory management system is ideal for large businesses and corporations that have warehouses and serious transportation logistics. It involves the use of software.
Items are constantly tracked and information about them is updated in real-time. This is because the software is often connected to points of sale, and it immediately sends data on the item’s availability and location.
These systems require special equipment, such as barcode scanners or radio frequency identification systems (RFID), which use fixed tag readers.
Use Plaky to streamline your inventory management
Regardless of how much inventory you have, it is vital to document each item, know where it is, and track how many items you have left.
Plaky is customizable and secure inventory management software.
It helps you manage your inventory, provides end-to-end tracking, and allows you to categorize your stock according to relevant categories. What’s more, you can get notified of any status change, so you and your team members are always up-to-date.
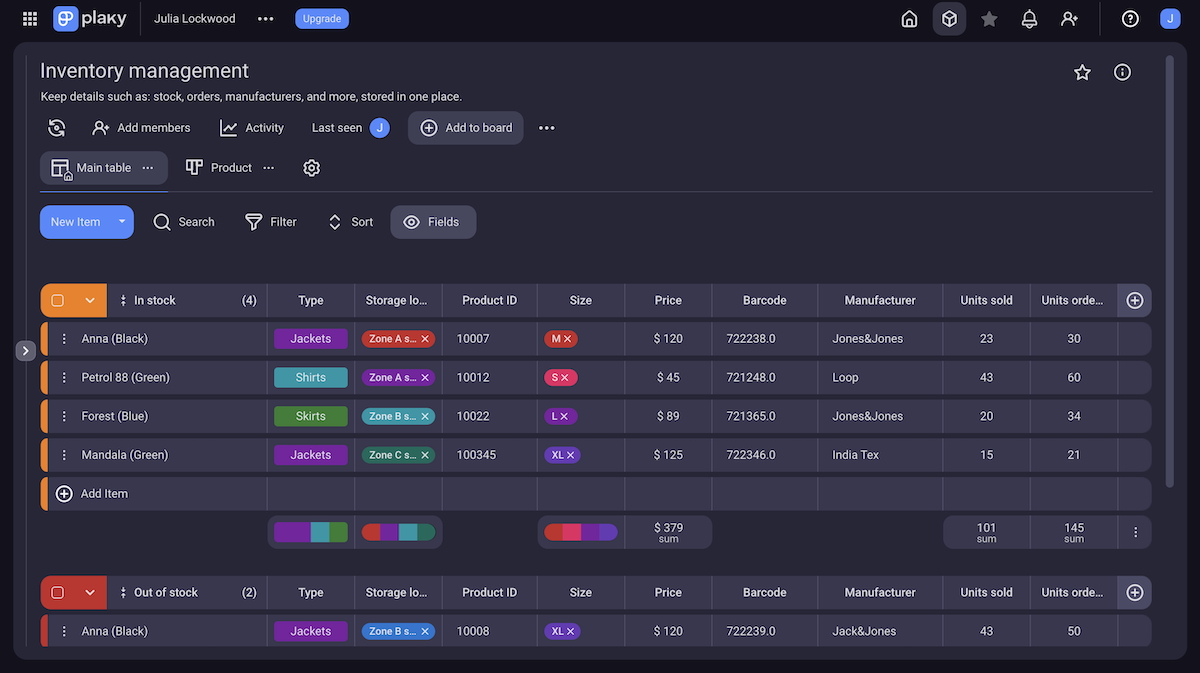
If creating a board from scratch sounds like too much work, you can make use of Plaky’s customizable inventory management template to get you started.
It can be adjusted to your needs, and you can keep data on product IDs, prices, invoices, and suppliers.
Plaky also provides many features that improve inventory management, such as:
- Customizable fields,
- Sorting boards for a clear overview,
- Unlimited number of files to share, and
- Unlimited users.
Besides inventory, Plaky can be used to track other resources as well — like your budget and human resources. Because of this, you can use it for effective resource allocation in general.
We mentioned retailers as the industry that needs inventory management most of all — they will also find Plaky useful for their operations. As great project management software for retail operations, Plaky can also be utilized in this specific industry.
As tracking inventory is most important in retail, using PM software can be much more beneficial and streamlined than spreadsheets, or pen and paper.
As you can see, inventory management software can be useful in many ways. It offers tools that can help you optimize your inventory type, deliver tasks, fulfill orders, and analyze financial data. So, help your inventory management improve and sign up for a free Plaky account today.