What Is the Six Sigma Methodology? The Ultimate Guide
At first glance, the Six Sigma methodology may look extremely complex. But after reading this guide, you’ll be able to navigate its complexities.
Whether you are already somewhat familiar with the Six Sigma project management methodology or you’ve just stopped by to brush up on your knowledge — you are at the right place.
In this guide, we will cover the following topics:
- The definition and purpose of Six Sigma,
- What Six Sigma is used for,
- What Lean Six Sigma is,
- Six Sigma principles and approaches,
- Six Sigma belts, champions, and executives,
- An example of Six Sigma,
- Six Sigma benefits, and
- The difference between PMP® and Six Sigma.
So, let’s get started.
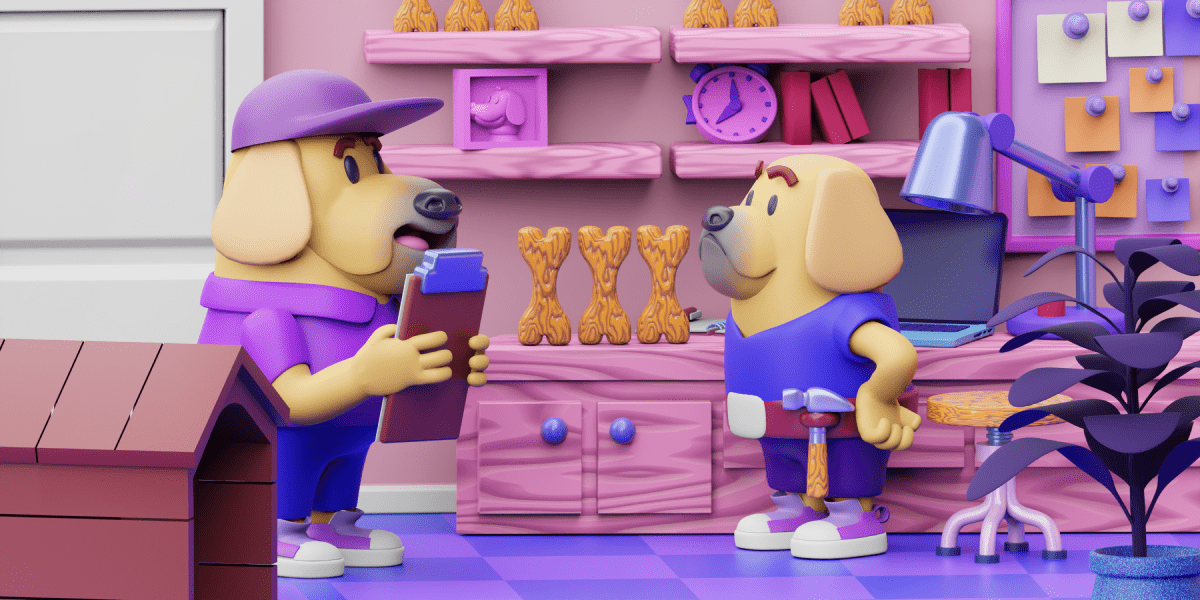
Table of Contents
What is Six Sigma methodology?
In simple terms, Six Sigma is a statistical and data-driven methodology businesses use to reduce or eliminate defects and improve processes.
Two engineers, Bill Smith (often called the ‘Father of Six Sigma’) and Mikel Harry, developed the Six Sigma methodology in 1986 while working at Motorola.
According to An Overview of Six Sigma by Montgomery and Woodall, after the Six Sigma implementation, Motorola managed to reduce defects on semiconductor devices by 94% between 1987 and 1993.
The same article highlights that the main objective of Six Sigma is “reducing variability in key product quality characteristics around specified target values to the level at which failure or defects are extremely unlikely.”
Six Sigma: What’s behind the name?
As explained in Six Sigma: A Complete Step-by-Step Guide, “6σ is a statistical representation for what many experts call a perfect process.”
Now, let’s explain why this methodology is called “Six Sigma”.
“Sigma” (sometimes represented with the lower-case Greek letter σ) in the Six Sigma methodology means standard deviation, while “Six” represents 6 standard deviations between average and acceptable specification limits.
The more standard deviations fit between process average and acceptable process limits, the less likely the process is to perform above acceptable limits and cause a defect.
In a Six Sigma process (6σ), there are only 3.4 defects per million opportunities. In other words, out of 1.000.000 opportunities for things to go wrong, only 3.4 things do go wrong.
In percentages, it means that 99.99966% of the products from a Six Sigma process are without defects.
At just one Sigma level below (i.e. 5σ), 99.977% of the products are defect-free, and there are 233 defects per million opportunities (DPMO).
The lower the number of σ (standard deviations), the higher the number of defects, and by extension, the higher the number of unsatisfied customers.
Let’s take a look at the table that displays the universal Six Sigma scale:
Sigma level | Defects per Million Opportunities (DPMO) | Percent Defects (%) | Percent Success (Yield %) |
---|---|---|---|
1 Sigma | 691,462 | 69 | 31 |
2 Sigma | 308,538 | 31 | 69 |
3 Sigma | 66,807 | 6.7 | 93.3 |
4 Sigma | 6,210 | 0.62 | 99.38 |
5 Sigma | 233 | 0.023 | 99.977 |
6 Sigma | 3.4 | 0.00034 | 99.99966 |
At very low Sigma levels, a process is unlikely to be profitable.
We will elaborate further on how to identify the Sigma level of your process and provide a more detailed Six Sigma scale in the Six Sigma example section.
Six Sigma definitions: What experts say
To explain Six Sigma in simpler terms, we’ve turned to experts.
One of our contributors is D. Lynn Kelley, Ph.D., a Senior Advisor to Brown Brothers Harriman Capital Partners, a member of the Board of Directors at Precision Terminal Logistics and Lean Enterprise Institute, as well as the author of the upcoming book Change Questions.
As a Six Sigma Master Black Belt, Dr. Kelley defines Six Sigma in the following way:
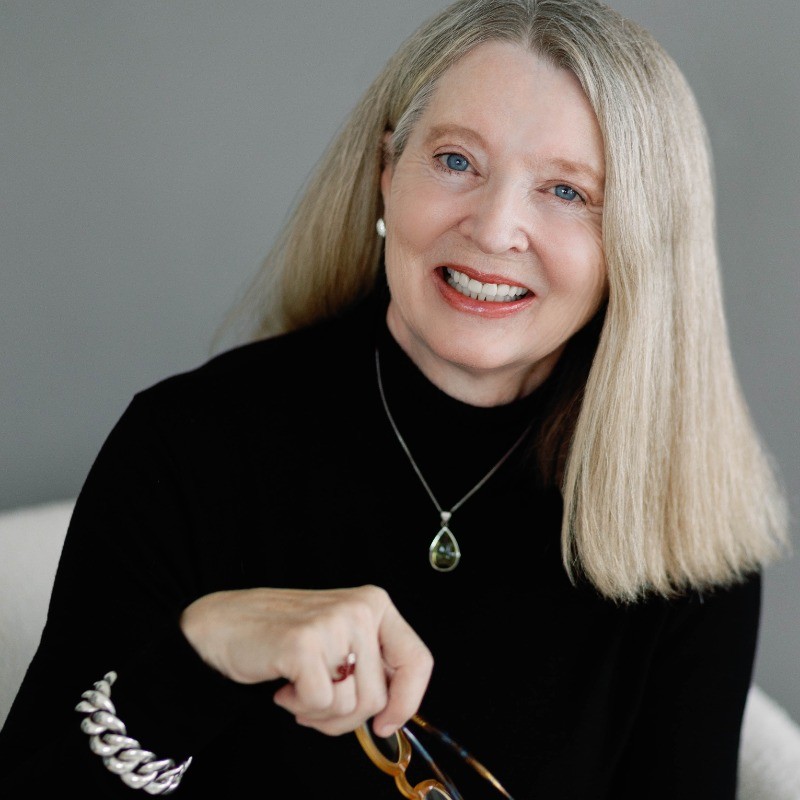
“Six Sigma is a sequential approach with each step adding value to the work done in the prior steps. Six Sigma’s foundation is the tried-and-true scientific method, giving Six Sigma credibility as a robust way to examine organizational problems. The focus while using Six Sigma is on the customer and all aspects of operational excellence. What differentiates Six Sigma from most continuous improvement methodologies is the emphasis on statistical analysis, making mini statisticians out of ordinary people.”
Another expert we’ve talked to is Marcos Clowes, a Chartered Fellow at The Chartered Institute of Logistics and Transport and a Six Sigma Black Belt. Here’s how Marcos defines Six Sigma:
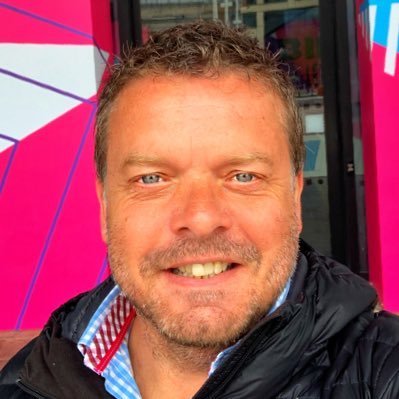
“Six Sigma is a disciplined and data-driven approach aimed at minimizing variations, defects, and errors in processes to achieve high levels of quality and efficiency. It involves using statistical analysis, problem-solving methodologies, and process improvement techniques to identify the root causes of issues and implement effective solutions.”
What is Six Sigma mainly used for?
Six Sigma is mostly used for increasing customer satisfaction and profitability by:
- Streamlining operations,
- Enhancing quality, and
- Eliminating defects in an organization’s processes.
According to Dr. Kelley, you can use Six Sigma for a variety of other purposes and industries, however, the method should be chosen with care as different projects call for different methods:
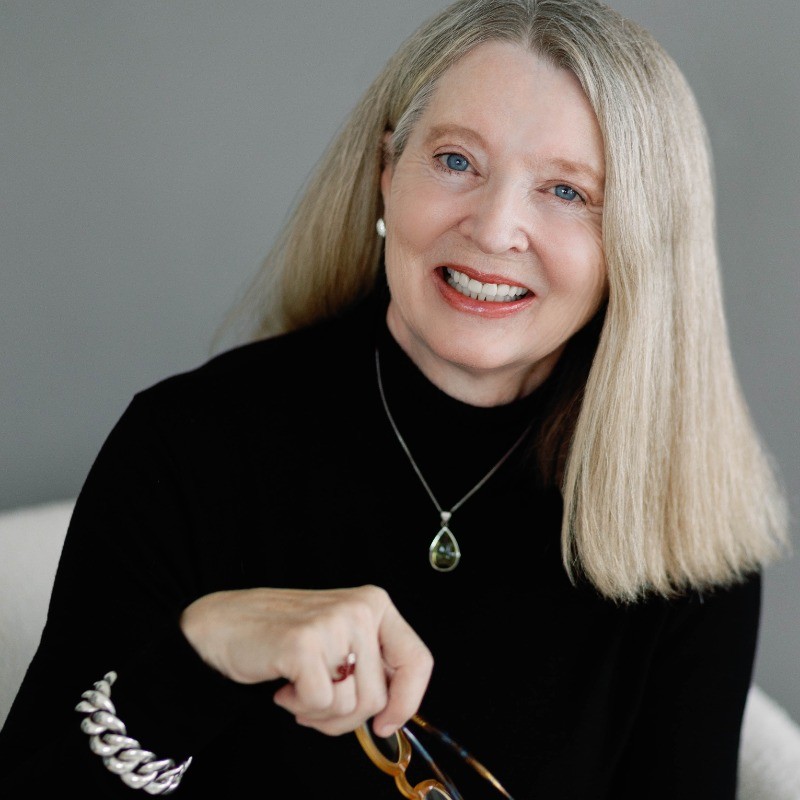
“Six Sigma applies to any industry, organization, or function and its reach extends well beyond the manufacturing industry. However, it does not apply to all types of projects. Applying Six Sigma to highly qualitative projects can result in elaborate contortions to squeeze a qualitative problem into something that is better met with anthropological/qualitative/observational methods. In addition, simple or straightforward problems can result in over-engineering either the analysis, the solution, or both.”
Clowes also claims that Six Sigma is a methodology suitable for various sectors and projects, listing some of them:
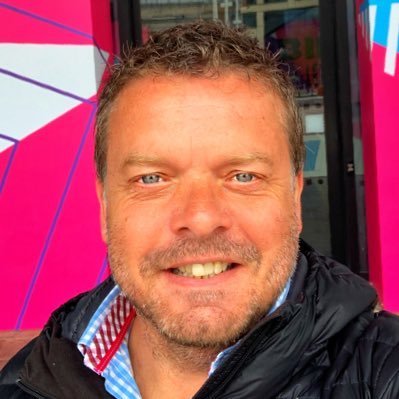
“Industries such as [the following] have adopted Six Sigma to improve:
- Healthcare,
- Finance,
- Information technology,
- Logistics, and
- Service sectors.”
What is Lean Six Sigma?
As explained in An Overview of Six Sigma, there’s an obvious connection between Six Sigma and Lean, as Lean manufacturing systems are designed to eliminate waste, such as rework or scrap, often resulting from excess variability.
A close connection between these 2 approaches results in the combination of the 2, i.e. the Lean Six Sigma concept.
Here’s how our contributor, Simon Elias, the Director of LCS (Lean Competency System), explains the basic Lean Six Sigma terms:
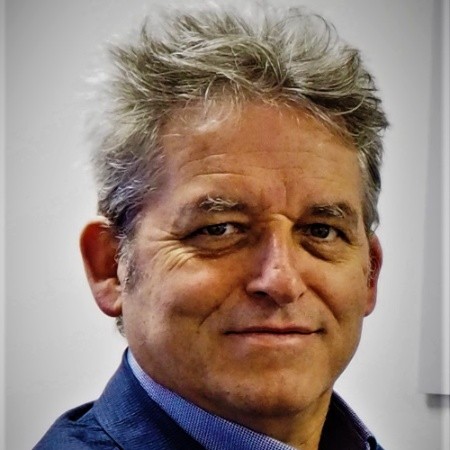
“The term ‘Lean Thinking’ covers the overall continuous improvement philosophy and Six Sigma is one of the methodologies that you can choose as an improver.
Six Sigma has its roots in manufacturing, many improvers see it as too narrow to use on its own — hence the term ‘Lean Six Sigma’ has arisen, which combines the best of both approaches.
By combining the two methods, you end up with a comprehensive toolset with greater results than can ordinarily be achieved by using Lean or Six Sigma individually.”
So, Lean Six Sigma is a data-driven approach that aims at improving performance by preventing defects and systematically reducing variation and waste.
💡Plaky Pro Tip
To learn more about Lean, take a look at our comprehensive guide:
What are the Six Sigma principles?
By following certain methodology principles, organizations can impact their Sigma level.
The most common Six Sigma principles include the following:
- Focus on the customer,
- Understand how work gets done,
- Focus on continuous process improvement,
- Reduce the variation,
- Eliminate waste,
- Provide training,
- Be flexible, and
- Control the process.
Let’s explain them in further detail.
Principle #1: Focus on the customer
The primary principle of Six Sigma is focusing on the customer.
By analyzing its offerings from the customer’s perspective, companies can improve the quality of their products.
As explained in Six Sigma: A Complete Step-by-Step Guide, the knowledge of customers’ needs combined with statistics, measurements, and process improvement methods may result in an increase in the following areas:
- Customer satisfaction,
- Customer retention,
- Customer loyalty, and
- Overall sales and profit.
Principle #2: Improve your data-gathering process
You should trace the process steps to determine waste areas and gather data to discover any specific problem areas you need to handle or transform.
But before you start gathering data, you need the following information first:
- Clearly defined goals for data collection,
- Purposes for data gathering, and
- Expected insights.
It is also necessary to ensure the accuracy of measurements and establish a standardized data collection system.
You can ensure measurement accuracy by verifying the following:
- Whether the data enables you to achieve your goals,
- Whether or not the data needs to be refined, and
- Whether you need any additional information.
Also, you can use project management software such as Plaky to keep track of all defects.
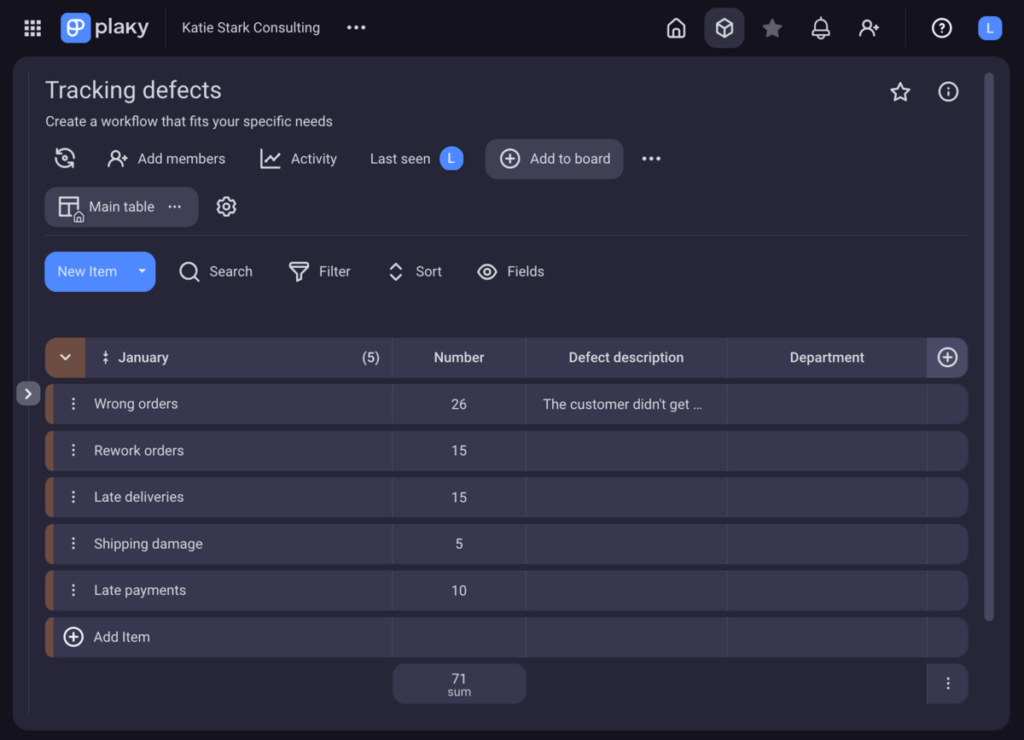
Using project management software allows you to organize all your business processes and track how well they’re performing and quickly determine which processes need your attention.
Principle #3: Focus on continuous process improvement
Six Sigma methodology is based on the concept of continuous improvement.
In other words, an organization practicing Six Sigma never stops improving.
Once it has improved one area, it instantly moves to another.
The goal is to reach the highest possible Sigma level for organizational processes — the Six Sigma level — with an accuracy of 99.99966%, while still maintaining other goals and requirements, such as financial stability.
The closer you are to the Six Sigma level, the better.
Principle #4: Reduce the variation
Simply said, variation is a lack of consistency.
Reducing variations improves the process leading to a more consistent customer experience.
Here’s an example to make the variation concept clearer:
Imagine running a burger bar and having 25 different burgers on the menu.
Your workers must know which ingredient combination goes into each burger and how many ingredients to use.
With many ingredient options available, there is a higher chance of errors occurring.
To reduce the variation, you can instruct your employees to use a certain amount of each ingredient for every burger.
Moreover, ingredients should always come from the same suppliers to avoid burgers tasting differently.
This way, you can ensure consistency in the final product as well as a more consistent customer experience.
Principle #5: Eliminate waste
Eliminating waste implies removing what’s unnecessary to improve the process outcome, and it may relate to:
- People,
- Actions, or
- Items.
Simply put, we should remove everything in the process that does not add to the customer’s value.
Eliminating waste reduces:
- Costs,
- Processing time, and
- Chances of errors.
At this point, you might be wondering how exactly are you supposed to know what should be eliminated.
To answer that question, take a look at the following example.
Imagine running a small pizza place.
To eliminate waste in your operations, you can ask yourself the following questions:
- Do I need 5 people to put the pizza together and serve it, or can a single person prepare a pizza while the others serve the customers?
- How many suppliers do I really need?
- Which pizza options are the most popular?
- Can I optimize the process by including only the best-selling pizzas in the menu and eliminating those nobody ordered in the previous 3 months?
- How much money do I spend on the ingredients for pizzas that are rarely ordered?
- How much money do I get from the best-selling pizzas compared to other pizza options I currently offer?
By identifying what is critical for your pizzeria, you will be able to find out what you can eliminate without compromising quality (and gain).
Principle #6: Provide training
The people on the team need to be trained and have knowledge of the Six Sigma methods of operation.
Forming a cross-functional team consisting of team members with various skills and expertise will help identify any variation.
Experts in different domains can analyze the processes from several angles as well as point out potential defects and discover solutions for them.
Principle #7: Be flexible
Six Sigma requires adaptability and having a flexible and responsive system.
Changes will inevitably happen as you eliminate faulty or inefficient processes.
Employees from all departments involved in the process should be able to adapt to these changes easily.
So, processes should be designed in a way that enables rapid and easy adoption.
For example, breaking down the processes into steps is a great practice.
This way, we can apply changes to the step that needs our attention, without having to change or adjust the entire process.
Principle #8: Control the process
As Six Sigma improvements deal with processes that are out of control, the goal is to bring those processes back within the state of statistical control.
After implementing improvements to your process, you can use certain tools to make sure the process remains in control, e.g.:
- Measurements,
- Statistics, or
- Other Six Sigma tools.
What are the 2 Six Sigma methodologies?
According to Six Sigma: A Complete Step-by-Step Guide, Six Sigma teams usually use the following 2 methodologies to make improvements and develop process controls:
- DMAIC (Define, Measure, Analyze, Improve, and Control), and
- DMADV (Define, Measure, Analyze, Design, and Verify).
Let’s explain what each methodology entails.
Approach #1: DMAIC
DMAIC is a Six Sigma approach to improving company processes, which doesn’t involve a complete redesign of the processes — only readjustments.
DMAIC in Six Sigma incorporates the following 5 phases:
- Define the problem, opportunities for improvement, project goals, and customer requirements,
- Measure how the process performs,
- Analyze the process to determine what causes poor performance (i.e. defects) and identify areas of improvement,
- Improve process performance by addressing and removing the causes of poor performance, and
- Control how the process is implemented in the future.
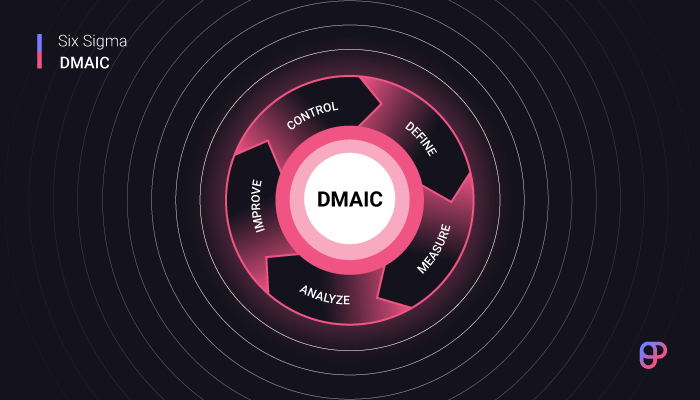
As Six Sigma is a data-driven methodology, the American Society for Quality recommends utilizing certain tools and techniques for the DMAIC process.
Let’s take a look at these tools in the following table:
DMAIC | Tools and techniques |
---|---|
Define | – Project charter – Voice of the customer – Value stream map |
Measure | – Process map – Capability analysis – Pareto chart |
Analyze | – Root cause analysis (RCA) – Failure mode and effects analysis (FMEA) – Multi-vari chart |
Improve | – Design of experiments (DOE) – Kaizen event |
Control | – Quality control plan – Statistical process control (SPC) – 5S – Mistake proofing (poka-yoke) |
Approach #2: DMADV
As sometimes, fixing or improving a process doesn’t solve the problem, organizations must instead completely replace or redesign processes to achieve desired goals.
In such cases, when developing a new product, service, or process, organizations may use a modified version of DMAIC called — DMADV.
The first 3 process steps of DMADV are similar to DMAIC, however, DMADV’s last 2 steps are oriented toward rolling out and testing a completely new process.
So, DMADV incorporates the following 5 steps:
- Define the purpose of a product, service, or project,
- Measure and determine the product, service, or process characteristics that are critical for their quality, including risk and production capabilities,
- Analyze the data you have to find the best design,
- Design the product, service, or process and test the prototype, and
- Verify the effectiveness of the design via simulations and a pilot program.
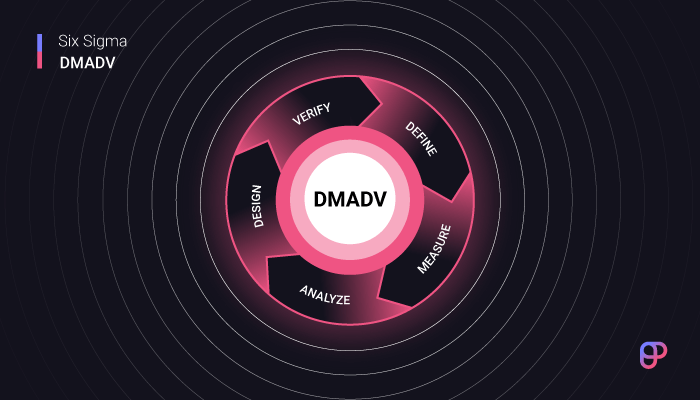
Now, let’s take a look at the tools and techniques most frequently used for DMADV.
DMADV | Tools and techniques |
---|---|
Define | – Project Charter – Critical to Quality (CTQ) measures – Voice of the customer |
Measure | – Control chart – Pareto chart – Histogram |
Analyze | – QFD – Prioritization matrix – FMEA |
Design | – Design of experiments – Action plan – TRIZ |
Verify | – Control chart |
Six Sigma belts, champions, and executives
Six Sigma has nothing to do with martial arts, though they have a couple of terms in common.
Namely, Six Sigma practitioners hold different color belts corresponding to the ones used in martial arts.
There are 5 types of Six Sigma certification levels and belts, including:
- Six Sigma White Belt,
- Six Sigma Yellow Belt,
- Six Sigma Green Belt,
- Six Sigma Black Belt, and
- Six Sigma Master Black Belt.
In addition to belts, there are 2 more Six Sigma roles that serve for setting the direction for selecting and deploying projects, including:
- Six Sigma Champions, and
- Six Sigma Executives.
Now, let’s analyze the belts and roles in more detail.
Six Sigma White Belt
White Belt holders are those with an elementary level of Six Sigma training.
A White Belt training is an excellent option for auxiliary staff members as it can help them understand why project teams work in a particular way.
According to the American Society for Quality, White Belts “can work on local problem-solving teams that support overall projects, but may not be part of a Six Sigma project team”.
Six Sigma Yellow Belt
The Yellow Belt certification is one step above the White Belt certification. Also, it’s an introductory position within Six Sigma.
Yellow Belts are regular project team members responsible for identifying processes that need improvement.
They work under the guidance of those with higher belt ranking — Green and Black Belts.
Six Sigma Green Belt
Certified Green Belts are Six Sigma team members who supervise the Yellow Belts and are usually under the supervision of Black Belts or Master Black Belts.
They assist with data gathering and analysis for Black Belt projects.
However, unlike Yellow Belts, they can lead smaller projects as well.
Six Sigma Black Belt
Certified Black Belts are Six Sigma project team leaders. They train and coach project teams.
Black Belts have the following responsibilities:
- Explain Six Sigma principles, including the supporting systems and tools,
- Demonstrate team leadership,
- Understand team dynamics,
- Delegate team member roles and responsibilities,
- Understand all aspects of the DMAIC model, and
- Have basic knowledge of Lean enterprise concepts.
As Marcos Clowes explains, Six Sigma Black Belts are also involved in data analysis and problem-solving:
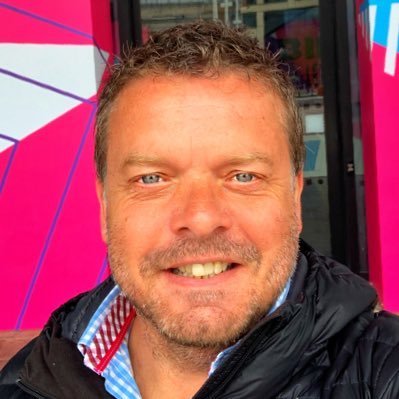
“Black Belts are skilled in statistical analysis and problem-solving techniques. They use data-driven methodologies to identify root causes of problems, analyze process performance, and make informed decisions based on the results.”
Marcos adds that Black Belts are also concerned with change management:
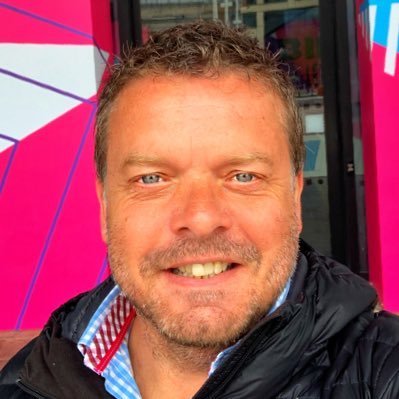
“Black Belts facilitate change management efforts by effectively communicating with stakeholders, managing resistance, and ensuring the successful implementation of process improvements.”
And, as Dr. Kelley highlights, “more effort must be placed on the change management side of the equation” within organizations.
Six Sigma Master Black Belt
Master Belts are the highest level Six Sigma in-house authorities who train and coach Green and Black Belts.
They are experts in the methodology, resources, and practices of Six Sigma.
As a Black Belt and Master Black Belt, Dr. Kelley shared some of the responsibilities she held within certain organizations:
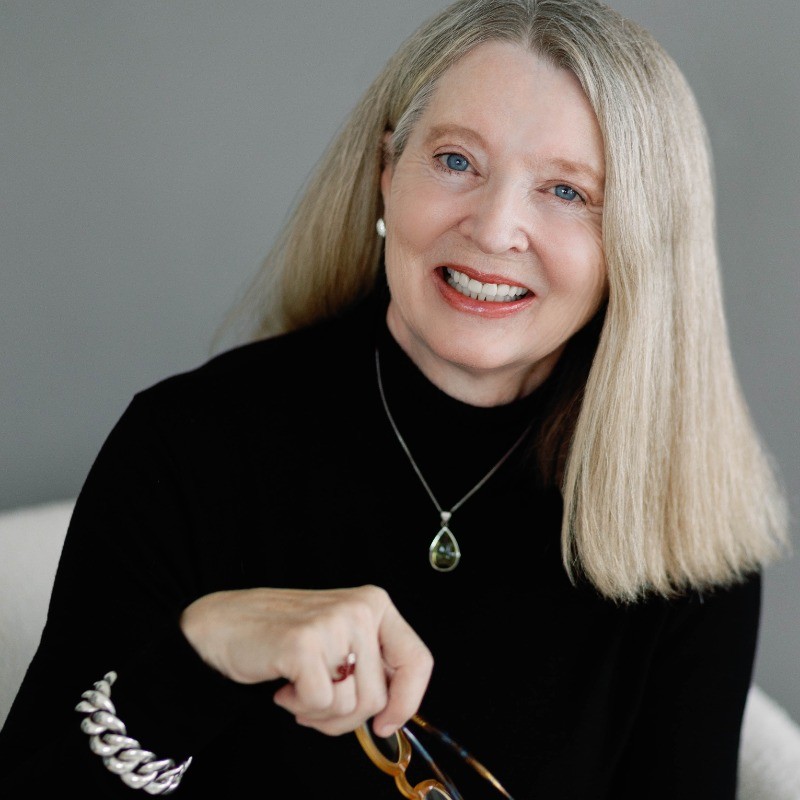
“I ran operational excellence/continuous improvement activities in 2 Fortune 200 companies, reporting directly to the CEO in both organizations. My role in the hundreds of ongoing projects in these organizations was to motivate, mentor, and demonstrate real results from Six Sigma and Lean. This included tracking metrics from all projects until they demonstrated at least six months of sustained improvement (at or above the project closure metric). From this, we calculated overall sustainment percentages and saw sustainment increase steadily until it reached 90% at one of the companies and 95% at the other.”
Six Sigma Champions
Six Sigma Champions are business leaders who translate the company’s mission, vision, and values into a Six Sigma deployment strategy that supports the company’s goals.
In addition, the champions have the following responsibilities:
- Guide the team,
- Remove obstacles that could hinder process success,
- Ensure the project is aligned with the company’s goals,
- Maintain team focus, and
- Ensure projects are completed on time.
Six Sigma Executives
Six Sigma Executives have the most training and experience. They hold the highest level in the Six Sigma hierarchy.
According to the American Society for Quality, Six Sigma Executives “provide overall alignment by establishing the strategic focus of the Six Sigma program within the context of the organization’s culture and vision.”
💡 Plaky Pro Tip
Interested in project management certifications? Check our comprehensive guide:
Now that you have mastered the Six Sigma basics, it’s time to show you how to determine the Sigma level of your process — with the help of an example.
An example of Six Sigma in project management
Suppose you run an online clothing shop and want to determine your current Sigma level.
Your company has received 11 customer complaints out of 580 orders made last week in total.
In that case, the number of orders is your sample size (580).
The number of complaints is the number of defects (11).
The complaints may be grouped based on the nature of each complaint, e.g.:
- Wrong color,
- Wrong size, or
- Wrong product type shipped.
All these categories represent opportunities for defects.
Now, let’s calculate your Sigma level.
Calculating your Sigma level
We can use the following formulas for the Sigma level calculations:
- Defects per unit
DPU = number of defects / number of units
- Defects per opportunity
DPO = number of defects / (number of units x opportunities per unit)
- Defects per million opportunities
DPMO = [number of defects / ( number of units x defect opportunities per unit)] x 1,000,000 or
DPO x 1,000,000
- Yield — the ability of a process to produce defect-free units
Yield = 1 – DPO
Now, let’s calculate the values based on the data we have.
Number of units: 580
Number of defects: 11
Opportunities per unit: 3 (size, color, clothing type)
DPU = number of defects / number of units
DPU = 11 / 580
DPU = 0.019
DPO = number of defects / (number of units x opportunities per unit)
DPO = 11 / ( 580 x 3)
DPO = 0.0063218391
DPMO = DPO x 1,000,000
DPMO = 0.0063218391 x 1,000,000
DPMO = 6,321.8391
Yield = 1 – DPO
Yield = 1 – 0.0063218391
Yield = 0.9936781609
Yield (%) = 99.36781609
Next, we have to take a look at the Yield to Sigma conversion table and identify our process Sigma level.
Yield % | Sigma | Defects Per Million Opportunities |
---|---|---|
99.9997 | 6.00 | 3.4 |
99.9995 | 5.92 | 5 |
99.9992 | 5.81 | 8 |
99.9990 | 5.76 | 10 |
99.9980 | 5.61 | 20 |
99.9970 | 5.51 | 30 |
99.9960 | 5.44 | 40 |
99.9930 | 5.31 | 70 |
99.9900 | 5.22 | 100 |
99.9850 | 5.12 | 150 |
99.9770 | 5.00 | 230 |
99.9670 | 4.91 | 330 |
99.9520 | 4.80 | 480 |
99.9320 | 4.70 | 680 |
99.9040 | 4.60 | 960 |
99.8650 | 4.50 | 1,350 |
99.8140 | 4.40 | 1,860 |
99.7450 | 4.30 | 2,550 |
99.6540 | 4.20 | 3,460 |
99.5340 | 4.10 | 4,660 |
99.3790 | 4.00 | 6,210 |
99.1810 | 3.90 | 8,190 |
98.9300 | 3.80 | 10,700 |
98.6100 | 3.70 | 13,900 |
98.2200 | 3.60 | 17,800 |
97.7300 | 3.50 | 22,700 |
97.1300 | 3.40 | 28,700 |
96.4100 | 3.30 | 35,900 |
95.5400 | 3.20 | 44,600 |
94.5200 | 3.10 | 54,800 |
93.3200 | 3.00 | 66,800 |
91.9200 | 2.90 | 80,800 |
90.3200 | 2.80 | 96,800 |
88.5000 | 2.70 | 115,000 |
86.5000 | 2.60 | 135,000 |
84.2000 | 2.50 | 158,000 |
81.6000 | 2.40 | 184,000 |
78.8000 | 2.30 | 212,000 |
75.8000 | 2.20 | 242,000 |
72.6000 | 2.10 | 274,000 |
69.2000 | 2.00 | 308,000 |
65.6000 | 1.90 | 344,000 |
61.8000 | 1.80 | 382,000 |
58.0000 | 1.70 | 420,000 |
54.0000 | 1.60 | 460,000 |
50.0000 | 1.50 | 500,000 |
46.0000 | 1.40 | 540,000 |
43.0000 | 1.32 | 570,000 |
39.0000 | 1.22 | 610,000 |
35.0000 | 1.11 | 650,000 |
31.0000 | 1.00 | 690,000 |
28.0000 | 0.92 | 720,000 |
25.0000 | 0.83 | 750,000 |
22.0000 | 0.73 | 780,000 |
19.0000 | 0.62 | 810,000 |
16.0000 | 0.51 | 840,000 |
14.0000 | 0.42 | 860,000 |
12.0000 | 0.33 | 880,000 |
10.0000 | 0.22 | 900,000 |
8.0000 | 0.09 | 920,000 |
Based on the table above, our Sigma level is between 3.90 and 4.
That means we can take certain actions to reduce the number of defects and achieve the best-case scenario, i.e. 3.4 DPMO.
Now, let’s calculate the number of defects for the Six Sigma process using the data we have.
Units: 580
Defect opportunities per unit: 3 (size, color, clothing type)
At the Six Sigma level, the number of DPMO (defects per million opportunities) is 3.4.
So, we can calculate the DPO (defects per opportunity) by using the formula for DPMO, as we already know the value for DPMO.
DPMO = 3.4
DPMO = DPO x 1,000,000
3.4 = DPO x 1,000,000
DPO = 3.4 / 1,000,000
DPO = 0.0000034
Now, we have the value for DPO, and we can use the formula for DPO to calculate the total number of defects.
DPO = number of defects / (number of units x opportunities per unit)
Defects = (units x opportunities per unit) x DPO
Defects = (580 x 3) x 0.0000034
Defects = 0.005916
Let’s compare our process performance at the current Sigma level to the one at the Six Sigma level.
Defects per million opportunities at the Current Sigma level (between 3.90 and 4) | Defects per million opportunities at the Six Sigma level |
---|---|
DPMO = 6,321.8391 | DPMO = 3.4 |
As we can see from the table, the number of DPMO is significantly lower at the Six Sigma level than the one we are currently at (between 3.90 and 4).
This further means that we might want to use the DMAIC approach to improve the process and try to reach the Six Sigma level.
What are the benefits of Six Sigma?
At this point, we’ll analyze the benefits Six Sigma brings to project managers, including the following:
- Better decision-making,
- Less waste,
- Improved quality and customer satisfaction,
- Decreased operational costs, and
- Increased productivity.
Let’s take a closer look at each benefit.
Benefit #1: Better decision-making
Without proper measurement and analysis, organizations often make bad judgments that lead to poor performance.
When applying Six Sigma, all decisions are data-driven, so you don’t need to rely on intuition or project assumptions.
Six Sigma enables better decision-making by relying on data analysis and improving processes based on measurements and metrics.
Having accurate data allows you to make the right choices and find the best solution for process improvement.
Furthermore, using Six Sigma helps organizations:
- Determine what is wrong,
- Validate their assumptions,
- Brainstorm potential solutions for problems, and
- Plan the necessary steps to avoid unwanted consequences.
Benefit #2: Improved quality and customer satisfaction
There is a direct connection between the quality of products and customer satisfaction — the better your products are, the more satisfied the customers will be.
Six Sigma helps reduce variations and defects, contributing to the better overall quality of products and services.
Benefit #3: Less waste
Six Sigma relies on a set of statistical tools to identify and validate a process’ root problem.
It helps your company optimize processes and decrease total waste.
Benefit #4: Lower operational costs
Organizations often spend extra time fixing defective products and dealing with dissatisfied customers.
By reducing problems to 3.4 DPMOs, Six Sigma significantly reduces expenses, as defective processes cost you money.
In other words, an efficient manufacturing process is less expensive, and Six Sigma makes it possible.
Benefit #5: Increased productivity
Applying Six Sigma to your processes boosts efficiency and allows for better project time management.
By identifying problematic areas and optimizing your processes, you help your teams operate more efficiently.
In addition, you avoid having the same problems repeat in the future and eat up your time, as Six Sigma helps you identify their roots.
What is the difference between PMP and Six Sigma?
While both the PMP® (Project Management Professionals) certification and Six Sigma focus on specialized strategies to create better business outcomes, their approach is different.
So, what are the main differences between PMP® and Six Sigma?
Let’s take a look at the following table.
PMP® | Six Sigma |
---|---|
Focuses on improving projects’ success rate. | Focuses on discovering and eliminating or reducing variations and defects within a specific process. |
A PMP® professional utilizes standardized practices to efficiently deliver a project that satisfies a predetermined goal. | A Six Sigma professional uses data-driven methods and statistics to pinpoint and solve problems. |
The focus is on completing a project within a specific project deadline. | Six Sigma projects have a continuous control phase. |
PMP® is the most industry-recognized certification for project managers. | Six Sigma is more commonly used in the manufacturing industry, where the methodology assists companies in achieving higher levels of product quality. |
PMP® professionals focus on how to plan and execute a project. | Certified Six Sigma professionals focus on improving processes. |
Requirements: — 4-year degree + 36 months of experience leading projects within the past 8 years + 35h of project management training, or — secondary education diploma + 60 months of experience leading projects within the past 8 years + 35h of project management training | Requirements vary based on the level of certification you’re pursuing. |
The PMP® certification is only available through the PMI (Project Management Institute). | The Six Sigma certification is available through several organizations. |
Even though PMP® and Six Sigma certifications are different, one doesn’t have to exclude the other.
Six Sigma professionals are great at discovering and solving problems, while PMP® professionals are experts at delivering projects.
Having individuals with both Six Sigma and PMP® certifications may be an excellent advantage for any organization.
💡 Plaky Pro Tip
Find out more about project management methodologies in the following guide:
Wrapping up: Six Sigma may significantly improve your business processes if you apply it to the right project in the right way
Six Sigma is a data-driven methodology that enables companies to achieve optimal business processes by identifying any weak points and acting on them.
By focusing on statistics, Six Sigma helps remove defects, reduce variations, and improve productivity, which ultimately leads to reduced costs.
In addition, Six Sigma emphasizes the value of focusing on customers’ needs with the aim of improving customer satisfaction.
Although Six Sigma to a great extent deals with statistical analysis, it’s important to remember that this methodology isn’t solely about the numbers, but also about the people involved in the process, or as Dr. Kelley explains:
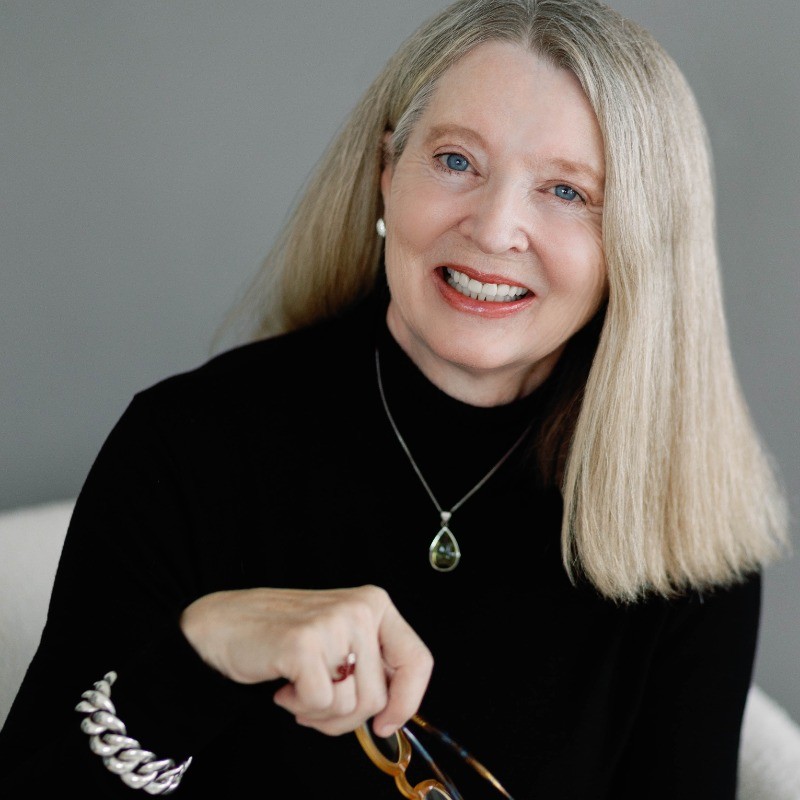
“Using statistics as a stand-alone way to address problems misses the broader sweep afforded by Six Sigma. Six Sigma has taught me to ensure that my data-driven approach includes more than just the process data at hand. The voice of the customer, insights and suggestions from the employees, and the impact upon the stakeholders are critical (and often ignored) in pure data-driven approaches.”
📖 Now that you’ve acquainted yourself with Six Sigma project management, dive further into other project management topics — check out our Project Management Glossary of Terms and read more about basic and advanced project management terminology.
References
- ASQ. (n.d.). The Define, Measure, Analyze, Improve, Control (DMAIC) Process. Retrieved April 26, 2022, from https://asq.org/quality-resources/dmaic
- ASQ. (n.d.-a). Six Sigma Belts, Executives and Champions. Retrieved April 28, 2022, from https://asq.org/quality-resources/six-sigma/belts-executives-champions#Roles
- Indeed Editorial Team. (2021, September 30). What Is DPMO and How To Calculate It (With Examples). Indeed Career Guide. Retrieved April 28, 2022, from https://www.indeed.com/career-advice/career-development/what-is-dpmo-and-how-to-calculate-it
- Indeed Editorial Team. (2021b, November 11). Six Sigma vs. PMP Certification: What’s the Difference? Indeed Career Guide. Retrieved April 28, 2022, from https://www.indeed.com/career-advice/career-development/six-sigma-vs-pmp
- International Six Sigma InstituteTM. (n.d.). History of Six Sigma. Retrieved April 29, 2022, from https://www.sixsigma-institute.org/History_Of_Six_Sigma.php
- International Six Sigma InstituteTM. (n.d.). What is Sigma and Why is It Six Sigma. Retrieved May 11, 2022, from https://www.sixsigma-institute.org/What_Is_Sigma_And_Why_Is_It_Six_Sigma.php
- iSixSigma-Editorial. (n.d.). Yield to Sigma Conversion Table. iSixSigma. Retrieved May 9, 2022, from https://www.isixsigma.com/new-to-six-sigma/sigma-level/yield-to-sigma-conversion-table/
- KnowledgeHut. (2022, March 14). PMP vs Six Sigma – How To Choose One. Retrieved April 29, 2022, from https://www.knowledgehut.com/blog/project-management/pmp-vs-six-sigma
- KnowWare International, Inc. (n.d.). DMADV Tools | Define Measure Analyze Design Verify. Retrieved April 27, 2022, from https://www.qimacros.com/lean-six-sigma/DMADV/
- Montgomery, D. C., & Woodall, W. H. (2008). An Overview of Six Sigma. International Statistical Review / Revue Internationale de Statistique, 76(3), 329–346. http://www.jstor.org/stable/2 7919650
- Ohio University. (2019, December 3). The 7 Roles of Six Sigma. Retrieved April 28, 2022, from https://onlinemasters.ohio.edu/blog/the-7-roles-of-six-sigma/
- Purdue University. (2021, December 28). DMAIC Vs. DMADV. Purdue University. Retrieved April 27, 2022, from https://www.purdue.edu/leansixsigmaonline/blog/dmaic-vs-dmadv/
- 6Sigma.com. (2019, June 24). Six Sigma Key Principles. 6sigma. Retrieved April 28, 2022, from https://6sigma.com/six-sigma-key-principles/
- Rongala, A. (2021, July 16). Six Sigma Calculations: A Brief Explanation. Invensis Learning Blog. Retrieved May 9, 2022, from https://www.invensislearning.com/blog/six-sigma-calculation/
- Rodriguez, D. (2020, September 2). A Beginner’s Guide to the Six Sigma Principles. Invensis Learning Blog. Retrieved April 21, 2022, from https://www.invensislearning.com/blog/six-sigma-principles-beginners-guide/
- The Council for Six Sigma Certification. (2018). SIX SIGMA A Complete Step-by-Step Guide (July 2018 ed.). https://www.sixsigmacouncil.org/wp-content/uploads/2018/08/Six-Sigma-A-Complete-Step-by-Step-Guide.pdf
- The Council for Six Sigma Certification. (n.d.). What is Six Sigma? Retrieved May 10, 2022, from https://www.sixsigmacouncil.org/six-sigma-definition/
- Villanova University. (2022, April 11). Difference Between Six Sigma and PMP® Certification. Retrieved April 29, 2022, from https://www.villanovau.com/resources/six-sigma/difference-between-six-sigma-and-pmp-certification/
- Villanova University. (2021, July 20). Project Management and Six Sigma – When to Use One or the Other or Both. Retrieved April 29, 2022, from https://www.villanovau.com/resources/project-management/project-management-and-six-sigma-when-to-use-one-or-the-other-or-both/