What Is Lean Project Management?
How has Toyota managed to produce high-quality cars for decades?
What’s their secret to successful production and organization of work?
The simple answer is — Lean management.
In this guide, we will go over:
- The 5 principles of Lean,
- Ways to implement Lean,
- Examples of Lean project management, and
- Advantages and disadvantages of Lean.
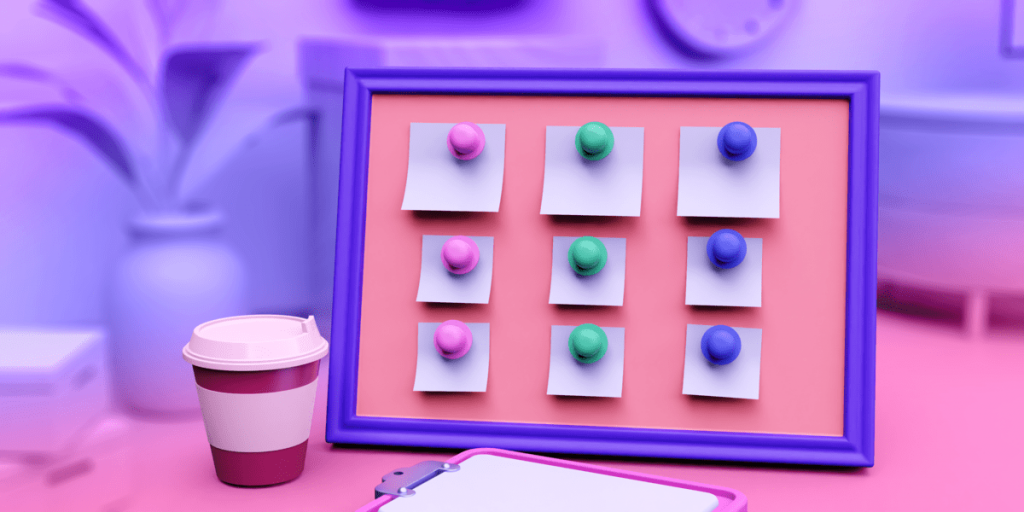
Table of Contents
What is Lean project management methodology?
Lean Enterprise Institute defines Lean as “a way of thinking about creating needed value with fewer resources and less waste” and “a practice consisting of continuous experimentation to achieve perfect value with zero waste”.
Lean was first developed in the form of a Lean manufacturing system in Toyota. Also called the Toyota Production System (TPS), this system is based on the just-in-time method of production (production of only what is needed for the next phase) and jidoka (translated as automation with a human touch).
In the 1990s, MIT researchers James P. Womack and Daniel T. Jones noticed Toyota was consistently able to achieve more with less.
They investigated why this was the case and presented their findings in The Machines That Changed the World (1990) and Lean Thinking (1996) — the latter being the first books to use the Lean moniker for codifying the set of 5 Lean principles as we know them today.
Lean project management is merely the application of Lean manufacturing principles to project management.
What are the 5 principles of Lean?
If we had to sum up Lean in a sentence, it would be this:
Deliver value from the customer’s perspective.
Maximizing this value is at the heart of all 5 principles of Lean.
Presented in an actionable manner, these principles state the following:
- Identify value,
- Create the value stream,
- Create flow,
- Establish pull, and
- Seek perfection.
We’ll explore each in more detail.
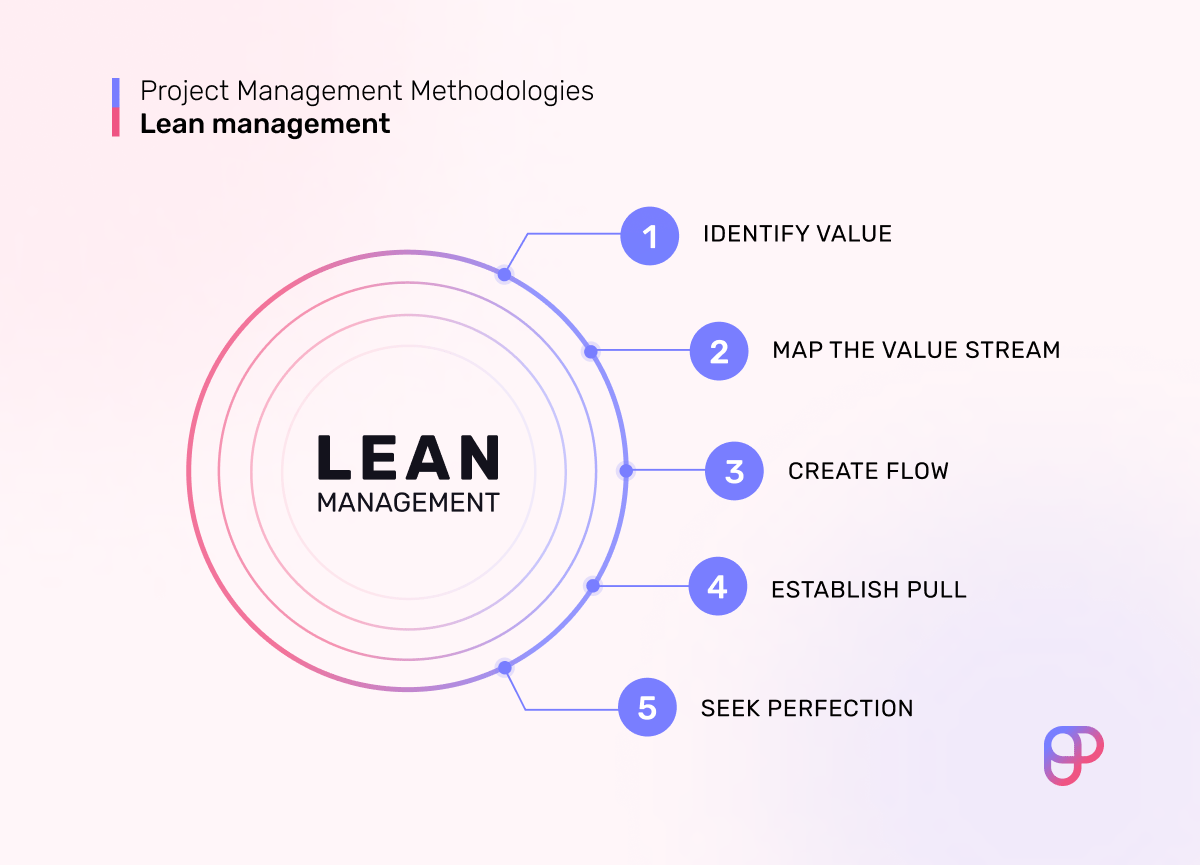
Principle #1: Identify value
In Lean project management, value is anything the customer is willing to pay for — be it a product or a service.
So, make sure you have a clear picture of what it is your customers want.
In the case of Toyota, their customers — car dealerships — want them to deliver cars to said dealerships.
That’s it.
The car dealerships don’t care how efficient the production line is or how much it costs to keep a large inventory of car parts.
Any costs accrued by inefficient production or oversized inventory are of no concern to the customers.
After all, none of this brings them additional value.
Costs that don’t add value to the customer are referred to as waste in Lean project management.
Principle #2: Create the value stream
Step 2 of Lean project management is eliminating waste, which is done by creating a value stream map.
A value stream map is used to visually represent the flow of value in your project.
Using a value stream, you can distinguish, at a glance, which steps in your production offer value and which only create waste.
Let’s take video production as an example. We’ll use exaggerated numbers to keep things simple.
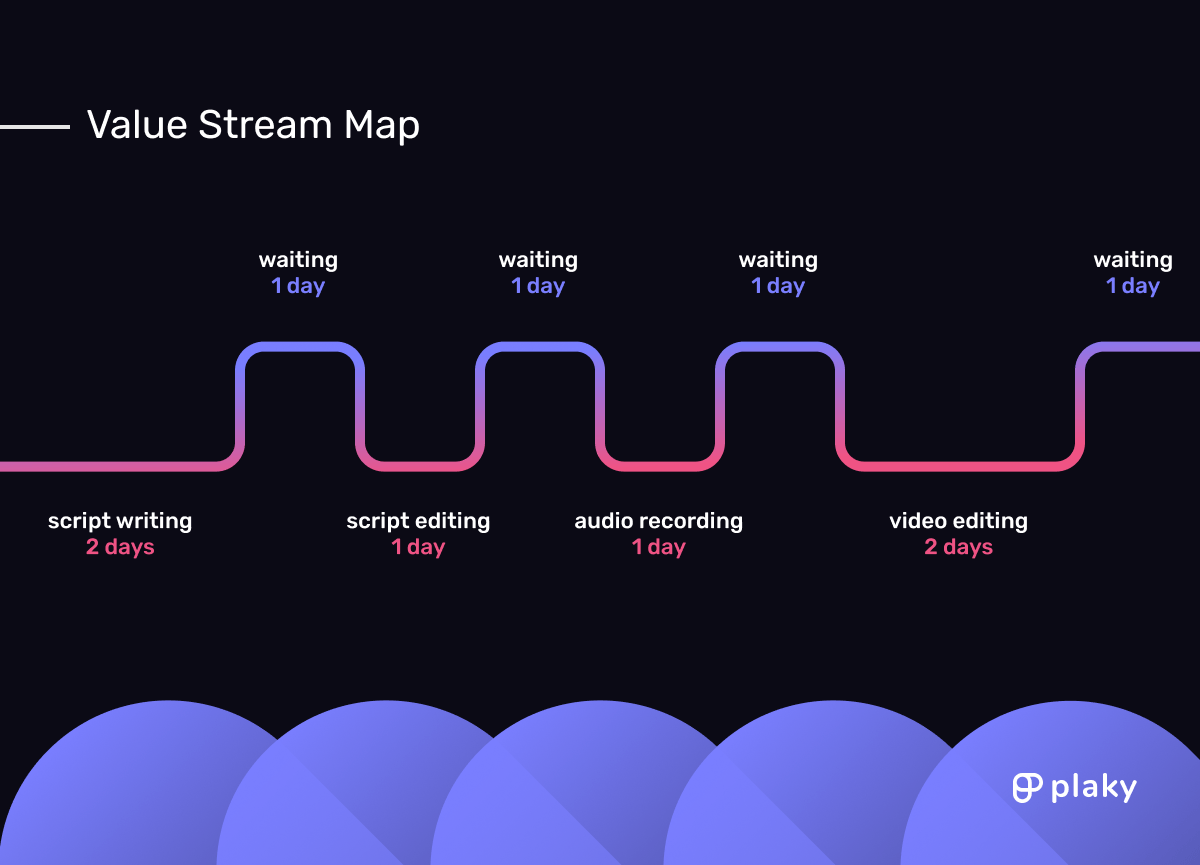
Let’s say the cycle time for this video production is 10 days:
- The content writer takes 2 days to write the script.
- They pass the script off to the editor through their PM software for video production, but 1 day passes before the editor takes a look at it.
- The editor takes 1 day to go over it.
- The editor sends the script to the voiceover artist, who also takes 1 day to start working on it.
- The voiceover artist takes 1 day to record the audio.
- The voiceover artist sends the audio file to the video editor, who takes 1 day to start working on it.
- The video editor takes 2 days to wrap everything up from the moment they start editing.
- The video gets uploaded the next day.
This is the general idea.
Now, let’s see — in this example, we have 6 days of activities that add value and 4 days of waste caused by waiting.
Waiting waste is just one of the many types of waste that can affect your project.
To help make you better at identifying waste, we’ll familiarize you with the waste terminology used in the Toyota Production System, i.e. the following 3 types of waste:
- Muda,
- Mura, and
- Muri.
Muda — a waste of resources
Muda refers to a waste of resources — something that doesn’t increase value from the customer’s perspective yet still costs you.
You can think of it as manufacturing waste.
In actuality, the term Muda (無駄) is the only one among these 3 that can be translated as waste — although a more common translation would be useless or futile.
Taiichi Ohno, the man behind the Toyota Production System, categorized the following 7 types of Muda:
- Overproduction,
- Waiting,
- Conveyance (transportation),
- Processing,
- Inventory,
- Motion, and
- Correction.
If you’re in doubt as to whether or not some of these processes constitute waste, simply ask yourself whether they provide value from the customer’s perspective.
Let’s circle back to the video production example mentioned earlier.
If, during the production of a video, it takes the video editor a whole day to start the editing process upon receiving the audio file, this day of waiting doesn’t add any value to the customer — from their perspective, being able to watch the video is the value.
Mura — waste caused by uneven workload
Mura refers to waste caused by uneven workload.
In Lean project management, the term Mura (斑) is correctly translated as uneven.
The idea is that uneven input is bound to result in uneven output, and uneven output is patently undesirable.
Those seeking to be Lean should make every effort to ensure their processes are standardized.
Going back to car manufacturing, let’s say the factory needs to transport 200 new cars to dealerships by rail, and they have 4 freight trains at their disposal. If they put 80 cars in the first freight train and 40 cars in the other 3, this would put uneven strain on the trains. The cars should be evenly distributed — 50 in each one.
Muri — a waste of effort
Muri refers to a waste of effort, generally brought about by overburdening workers or equipment.
Although often mistranslated as overburden in the context of Lean project management, the 2 kanji used to depict Muri (無理) are most accurately translated as unreasonable.
The idea is that overburdening people and equipment is unreasonable, as it inevitably leads to burnout and malfunctions.
This, in turn, leads to errors that detract from the value of your project. And, anything that detracts from value is anti-Lean.
Principle #3: Create flow
Identifying and removing waste is only half the work.
The other half is reconfiguring your workflow to function without waste.
If you’ve been wasting a lot of resources by keeping an unnecessarily large inventory, you can’t just say “We’ll keep less inventory” — that’s half the work.
Instead, you need to take a systemic approach to reevaluating and reconfiguring your inventory management.
If you’re renting a large storage facility and you start keeping less inventory, your storage facility should be made to reflect this change. After all, keeping storage space is expensive in and of itself.
Alternatively, if you’re making cars and you’ve discovered the production line moves the chassis around too much, you can’t just stop moving the chassis — this would bring production to a complete halt.
Instead, you need to create a new production line that will maximize the value flow without unnecessary movement.
Principle #4: Establish pull
The 4th principle of Lean instructs us to establish a pull system.
Just in case you’re unfamiliar with the terminology of pull and push systems, here’s a brief explanation:
- In pull systems, production is initiated in response to customer demand.
- In push systems, production is initiated in anticipation of customer demand.
A simple example of a pull system is a print-on-demand business. Only when a customer places an order, does the business create the product — print a book, a shirt with a logo, or something similar. So their production is a direct response to customer demand.
In Lean project management, pull systems are used to ensure your supply closely matches the demand for your product.
That’s because — looking from the eyes of the consumer — overproduction is a waste.
One of the simplest ways to introduce pull into your projects is by using the Kanban project management framework.
Kanban operates by severely limiting the work in progress — i.e. the number of tasks — each worker is allowed to work on at the same time.
This ensures workers focus all their efforts on the work at hand and only start working on a new task once they’ve finished the previous one.
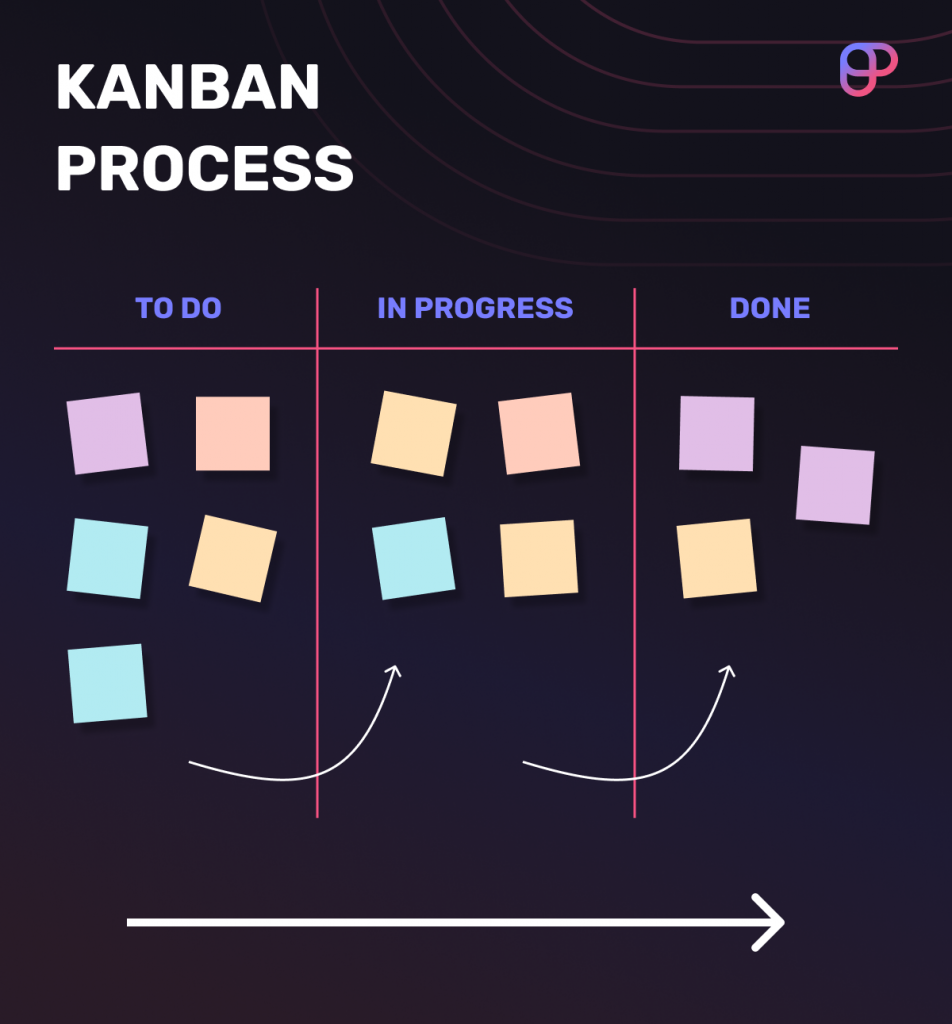
Kanban and Lean are somewhat related anyway, with both finding their roots in Toyota.
This is to say that Toyota, the progenitor of Lean manufacturing, uses Kanban as an integral part of their Toyota Production System.
Principle #5: Seek perfection
Lastly, it’s important to note that Lean project management is a continuous process.
It entails continuously reevaluating your processes and seeking ways to optimize them even further.
There is no room for complacency in Lean project management.
How do you implement Lean project management?
Implementing Lean means adhering to the 5 principles of Lean.
So, in this section, we have included some tips to help you implement the said principles:
- Conduct introspective analysis,
- Implement Lean gradually, and
- Use Lean project management tools.
Tip #1: Analyze and upgrade processes
Once you’ve defined value, you should analyze the current processes and procedures of your project.
In other words, you should check to see which parts add value and which parts add waste.
Then, revamp the process to keep it functional while removing as much waste as you can.
Unfortunately, it’s hard to be more specific here, as there’s no telling which types of waste a certain project will suffer from.
The best thing you can do is map out the value stream and check for the 7 types of Muda, as well as Mura and Muri.
Tip #2: Implement Lean gradually
Although eliminating waste is a positive change, too much change at once can be a shock to the system.
So, it’s a good idea to implement Lean gradually, especially if you have a large organization.
Try implementing it 1 department at a time or 1 production line at a time. This will allow you to see if the changes are effective, and it will give your employees time to get used to them.
Tip #3: Use Lean project management tools
Once you’ve figured out a way of eliminating waste and maximizing the value you bring to the customer, it’s time to implement a pull system.
The best way to do this is by utilizing a Lean project management tool like Plaky.
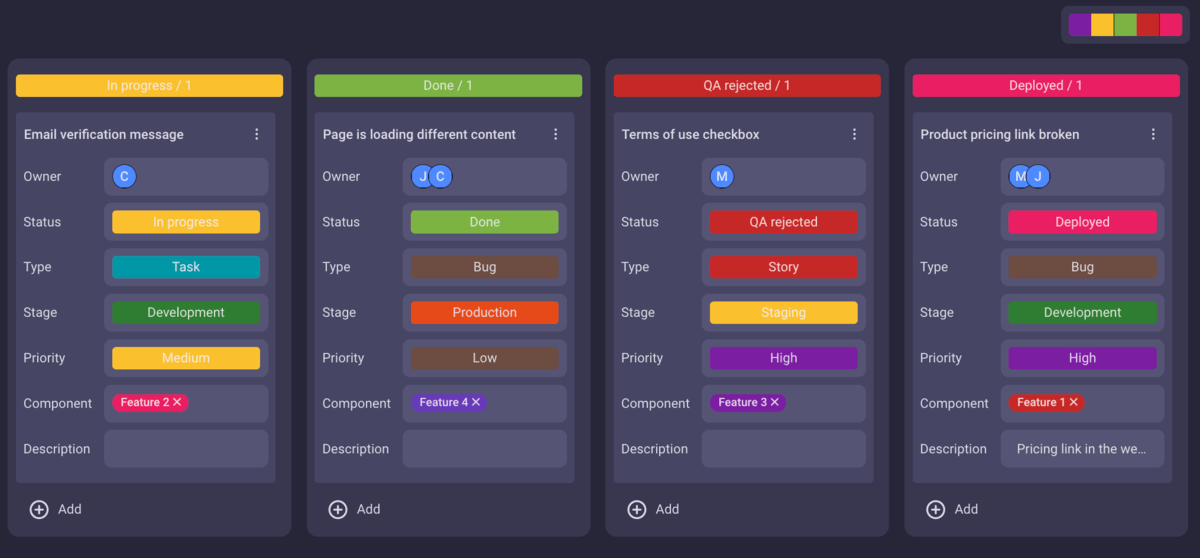
Plaky allows you to organize all tasks using customizable Kanban boards, which ensures that your workflow is pull-centric, regardless of the size of your project.
3 Lean project management examples
Lean may have started in manufacturing, but it can be found in various industries. Here are examples of how Lean project management can be implemented in:
- Restaurant service,
- Healthcare, and
- Software development.
Example #1: Restaurant service management
You have likely witnessed a well-implemented Lean approach without even realizing it.
Restaurants are a good example of implementing Lean project management principles with great results:
- Identify value — the value for customers in restaurants is a tasty meal that arrived promptly.
- Create the value stream — service in restaurants is very dynamic, and there is no room for waste. They eliminate waste of inventory by keeping only the ingredients they need in the near future (they can’t stock up too much in advance since the food can go bad). Waste of waiting is also minimal in restaurants — the food can’t be left waiting too long since it can cool or melt.
- Create flow — for the reason mentioned above, the process of service in restaurants has to work like a well-oiled machine: cook ➡ waiter ➡ customer.
- Establish pull — they produce meals as the customers order them, contrary to push systems of fast food joints that prepare food (like pizza or french fries) in advance.
- Seek perfection — restaurants always have to strive to improve and optimize their service.
Example #2: Healthcare
If there is one place where we want everything to function without a glitch, it’s the hospital. So, although healthcare may not be the first industry that comes to mind in connection to Lean practices, it can definitely benefit from implementing Lean.
Let’s look at how going Lean in the NHS (UK’s National Health Service) and implementing the 5 principles might make them more functional:
- Identify value — the value for the NHS is the patient’s health, well-being, and experience. This includes not getting an infection while in the hospital, not waiting in cues, etc.
- Create the value stream — the staff work together to identify waste and see how the system can be improved. Some examples of waste include: waiting for results, inventory waste like unnecessary stock, requesting unnecessary tests, etc.
- Create flow — the hospital must organize its processes to ensure a smooth flow of patients. For example, admission and discharge processes should be standardized. Also, the stock should be organized according to the frequency of use.
- Establish pull — the system should be organized so that it pulls patients through the processes. For example, the usual practice in the NHS is that emergency patients are pushed onto wards, where staff are forced to search for available beds for them. It would be better if wards would pull patients from the emergency rooms instead. This would save time and consequently cut delays, increase productivity and speed up processes.
- Seek perfection — as healthcare is constantly advancing, hospitals should always look for new and better ways to provide value to patients.
Example #3: Software development
Lean project management has found its way into software development, where it’s evolved and slightly altered the original 5 principles.
The Lean approach to software development was defined in the book Lean Software Development: An Agile Toolkit by Mary and Tom Poppendieck. They identified 7 principles for Lean software development:
- Eliminate waste — waste in the sense of software development refers, among other things, to extra features and processes, task switching, and partially done software.
- Amplify learning — this means that everyone should be allowed to contribute, and knowledge should be shared among the project stakeholders, e.g. by facilitating feedback from the clients, organizing meetings, etc.
- Decide as late as possible —this principle allows you to delay irrevocable decisions until the last responsible moment, that is until delaying has negative consequences. For example, you can delay the decision on which features to include in the free plan of your app until you do sufficient market research.
- Deliver as fast as possible —software development is a fast-changing environment, so you have to keep up. You can achieve this by introducing a pull system, reducing cycle time, and providing developers with the financial information about the business (which products bring the most profit for example).
- Empower the team — you should create an environment where workers are motivated to contribute, aren’t afraid of making a mistake, and are able to actively take part in improving work. The development team should also be in contact with the customers to enable them to better understand their needs.
- Build integrity in — to keep the integrity of your business, you should focus on your customer’s demands and create a functional, high-quality product.
- See the whole — you have to incorporate Lean into the entire workflow, even including the contracts with customers to ensure they support collaboration.
Advantages of Lean project management
The biggest benefits Lean brings to projects are:
- Reduced costs,
- Shorter time frame,
- Higher customer satisfaction, and
- Improved employee experience.
Advantage #1: Lean reduces costs
Identifying and eliminating waste in your project workflow is guaranteed to reduce overall costs.
If we look back at the 7 Muda, these are all processes that don’t add value but cost resources:
- Needless transportation — costs both time and money,
- Overproduction — freezes up your business equity in inventory that exceeds demand, and
- Keeping a large inventory — as mentioned, is simply a pricey endeavor.
We could go on.
The point is that the biggest advantage of using Lean is its ability to maximize profits by eliminating unnecessary costs — and it works.
💡 Plaky Pro Tip
Learn more about handling costs in project management in our articles:
Advantage #2: Lean saves time
All types of Muda cost you time. Although waiting is the most obvious waste of time, all other types ultimately lead to wasting your time as well.
You can save valuable time by eliminating unnecessary processing, transportation of products, and motion.
For example, if the warehouse with the parts needed for assembling your product is far away from the production line, not only are you wasting money on transportation, but you are also wasting time on it.
Without wasting time on unnecessary tasks, you can produce more in less time, meaning productivity is on the rise.
💡 Plaky Pro tip
Discover why time management is a crucial part of managing projects:
Advantage #3: Lean increases customer satisfaction
Since Lean focuses on delivering value from the customer’s perspective, it stands to reason that Lean practices lead to higher customer satisfaction.
It’s important to make sure that waste reduction reduces only the costs of production while leaving the quality of the product as is.
Advantage #4: Lean improves employee experience
If you want to have a successful business with experienced and expert employees, positive employee experience is vital.
The elimination of Muri (waste of effort) and Mura (waste caused by uneven workload) helps create a healthy work environment.
The employees are not overburdened with work, which means there is a lower chance of burnout.
Disadvantages of Lean project management
For all of its advantages, however, Lean project management also comes with several hidden disadvantages you should be aware of.
The 2 major disadvantages of Lean are:
- Little room for error, and
- Counterproductive results
Disadvantage #1: Lean leaves little room for error
In a sense, Lean is all about producing the desired results with the minimum investment:
- Minimum workforce,
- Minimum equipment,
- Minimum transportation, and
- Minimum everything.
Your goal is to do just enough work, just in time to provide value to the customer.
This shouldn’t be confused with delivering a subpar quality product or service — it should be free of any defects.
But, the goal is to use the minimum input needed for the desired output.
In theory, this sounds great.
And, in practice, it does work.
But, using Lean leaves you with very little room for error.
Taken to its extreme, progress on a Lean project can be compared to walking on a tightrope, where 1 misstep can cause serious issues.
Even though Lean teaches us not to overburden equipment, breaks and malfunctions still happen. And, with no redundancy, they can completely halt the progress of a project.
This 1 disadvantage can have a range of consequences, like missing deadlines or producing defective products.
Disadvantage #2: Lean can lead to counterproductive results
The initial return on investment for using Lean is typically great.
This is most noticeable when low profits caused by inefficiencies serve as the impetus for a project or production to switch to Lean.
That first batch of waste elimination and value flow reconfiguration tends to have universally positive effects:
- The customers are happy — they receive more consistent value,
- The workers are happy — they work more efficiently instead of just working more, and
- The leaders/management are happy — they reduce costs and increase profits.
But, Lean is a process of continuous improvement.
And, it’s not uncommon for leadership to get drunk on the potential improvements of subsequent value flow reconfigurations.
When performed in quick succession, these reconfigurations bring diminishing returns, while frustrating the workers.
For someone new to Lean, the costs of continuously reconfiguring the value flow can greatly exceed the benefits.
This is a waste of resources and therefore counterproductive to the goals of Lean.
This happens when overzealously tracking productivity and waste starts to negatively affect production, turning a means to an end into an end unto itself.
Now, you shouldn’t take this as advice to forget all about the 5th principle of Lean — seeking perfection.
Just make sure the improvements you make are as beneficial in practice as they are in theory.
What’s the difference between Lean and Agile project management?
Rather than being concrete project management methodologies, both Lean and Agile are best thought of as project management mindsets:
- Lean teaches you to deliver value from the customer’s perspective by cutting down on waste and aiming to accurately meet the demand for your product or service.
- Agile (to oversimplify it) teaches you to take an iterative and flexible approach to managing projects by making sure to incorporate customer feedback into the production/development process. For a more detailed explanation, it’s best to refer to our guide on Agile project management.
Interestingly enough, Lean and Agile aren’t mutually exclusive.
You can be both Lean and Agile at the same time.
Standing testament to this is Kanban, which is, at the same time, an Agile framework and one of the best ways to integrate a pull system mandatory for Lean project management.
Looking at Toyota’s 6 rules of using Kanban, we can see they perfectly complement Lean:
- “Never pass on defective products”
- “Take only what is needed”
- “Produce the exact quantity required”
- “Level the production”
- “Fine-tune production”
- “Stabilize and rationalize the process”
In this sense, you can think of Kanban as the intersection where Agile and Lean — 2 otherwise different project management paths — meet.
Conclusion: Lean allows you to achieve more with less
With 70 years of history through the Toyota Production System, Lean project management is a proven way to increase value and reduce costs by eliminating waste and utilizing a pull system.
This is beneficial not only for startups, who cannot afford to waste any resources but also for well-established companies seeking to improve their profit by cutting costs without sacrificing quality.
📖 If you’re interested in learning more about project management and like your information presented in a comprehensive and easy-to-understand manner, check out our Project Management Glossary of Terms.
References:
- Bubernak, C., & Schweikert, M. (2012, March 23). Lean Software Development. University of Colorado. https://home.cs.colorado.edu/~kena/classes/5828/s12/presentation-materials/schweikertmarcbubernakchris.pdf
- Crawford, M. (2016, March 9). Five Lean Principles Every Engineer Should Know. ASME. https://www.asme.org/topics-resources/content/5-lean-principles-every-should-know
- Lean Enterprise Institute (n.d.) 7 Wastes. Retrieved July 31, 2023, from https://www.lean.org/lexicon-terms/seven-wastes/
- Lean Enterprise Institute. (n.d.). Pull Production. Retrieved May 4, 2022, from https://www.lean.org/lexicon-terms/pull-production
- Lean Enterprise Institute (n.d.) What is Lean? Retrieved July 31, 2023 from https://www.lean.org/explore-lean/what-is-lean/
- Purdue University. (2021, May 30). Value Stream Mapping: The Search for Adding Value and Eliminating Waste. https://www.purdue.edu/leansixsigmaonline/blog/value-stream-mapping/
- Toyota Production System. (n.d.) Retrieved July 31, 2023. https://www.toyota-europe.com/about-us/toyota-vision-and-philosophy/toyota-production-system
- Toyota Production System. (n.d.) Retrieved July 31, 2023. https://global.toyota/en/company/vision-and-philosophy/production-system/
- Toyota UK Magazine. (2013, May 31). Muda, Muri, Mura — Toyota Production System Guide. https://mag.toyota.co.uk/muda-muri-mura-toyota-production-system/
- Toyota UK Magazine. (2013, May 31). Kanban — Toyota Production System guide. https://mag.toyota.co.uk/kanban-toyota-production-system/
- Westwood, N., James-Moore, M., & Cooke, M. (n.d.) Going lean in the NHS. https://www.england.nhs.uk/improvement-hub/wp-content/uploads/sites/44/2017/11/Going-Lean-in-the-NHS.pdf