What Is Cost Variance? Formula, Types, & Examples
Cost variance is a project management concept used to keep a project’s budgeted costs on track. As the budget is one of the most important elements of a project, project managers should calculate the cost variance throughout the project’s life cycle.
Below, we will define cost variance, explore the importance of cost variance analysis in project management, and show you how to use various cost variance formulas to calculate it as the project progresses.
You’ll also see cost performance values illustrated through practical examples and get tips on how to keep projects on the right track.
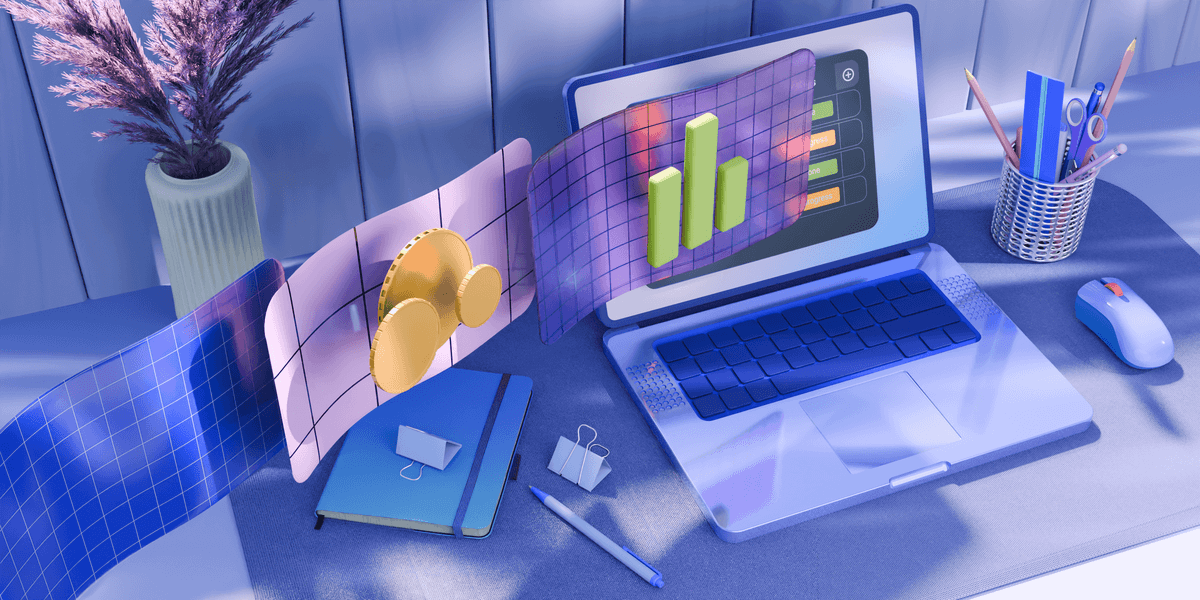
- Cost variance is the difference between the estimated and actual project cost.
- Calculating cost variance requires knowledge of earned value and actual costs.
- There are 3 outcomes when calculating cost variance: positive, zero, and negative.
- You can calculate cost variance for several consecutive periods, at a particular point in time, or at the end of a project.
Table of Contents
What is cost variance?
Cost variance is the difference between a project’s expected and actual cost at a given point in time.
Cost variance (CV) is calculated as the difference between the earned value (EV) and the actual cost (AC) of a project.
This calculation can be performed at any point during the project’s development to check whether the project is on, under, or over the planned budget.
Cost variance is one of the key elements of earned value analysis (EVA), which you can use to evaluate a project’s performance and progress.
💡 Plaky Pro Tip
Earned value analysis and its key dimensions are a part of earned value management (EVM), a performance management methodology. To learn more about EVM, check out this guide:
How to calculate cost variance in project management
The cost variance formula helps you determine the difference between the budgeted cost of work performed (BCWP) and the actual cost of work performed (ACWP). These parameters are also known as earned value (EV) and actual cost (AC).
Earned value is defined as the monetary value of work performed, while actual cost is the money spent on the work performed at a given point in time.
The difference between these 2 parameters shows if there is a cost variance. So, the formula for cost variance is:
CV = EV – AC
You can get the value of AC by simply adding up all the costs. To calculate EV, use this formula:
EV = % of work completed x total project budget
To calculate how much a project is over or under budget in percentages, use this cost variance formula:
CV % = (EV – AC) / EV
Positive vs. negative cost variance
The main purpose of calculating the cost variance is to see whether the project expenses are under control and how well the project is performing financially.
A big part of project cost control is figuring out how much the actual cost has deviated from the cost baseline and what caused the variance.
Ideally, the cost variance of a project should be zero, meaning that the expenses haven’t strayed from their planned value. However, this rarely happens as not every project always goes according to plan.
Instead, we can distinguish between a positive (favorable) and a negative (unfavorable) cost variance.
A favorable cost variance occurs when project expenses are below the budgeted value at a certain point in time. A positive cost variance is usually a good sign. Still, project managers should investigate whether it is a result of falling behind the project schedule.
In contrast, an unfavorable cost variance indicates the project is currently over budget, meaning that project managers should look into the unfavorable result and take corrective actions.
We can apply the cost variance formula to different budget categories and types of project costs to determine where we stand financially. That way, we can pinpoint exactly where the positive or negative cost variance has occurred.
Cost variance examples
Let’s illustrate the concept of cost variance and its results with examples so that you can better understand this cost performance measurement.
Example #1: Negative cost variance
Imagine you need to build a garden fence. Your budget is $4,000, and you have 5 days to build it.
Today is day 4. You’ve spent $3,300, but only did 75% of the work because you had to go to the store to get a new spade and some screws.
Clearly, everything didn’t go according to plan, and you want to check the cost variance to see where your project stands.
Actual cost (AC) = $3,300
Earned value (EV) = $4,000 x 75% = $3,000
Cost variance (CV) = EV – AC = -$300
The actual cost is the amount you have spent on the project so far, while the earned value is the value of work performed.
If the actual cost is greater than what the cost should have been, the variance is labeled as negative. In this case, the result shows your project is over budget by $300.
Example #2: Zero cost variance
Let’s say that you’ve hired a team to renovate your master bathroom. The renovation should cost $8,000, including all the necessary materials. The team has 10 days to complete the project.
By the end of day 5, the team has completed 50% of the work. So far, you’ve spent $4,000 on the renovation.
In this case, the project is right on track. Here’s why:
Actual cost (AC) = $4,000
Earned value (EV) = $8,000 x 50% = $4,000
Cost variance (CV) = EV – AC = $4,000 – $4,000 = $0
The project is financially doing well and is neither over nor under budget.
When the actual cost is equal to the planned budget, there is zero cost variance.
Example #3: Positive cost variance
You’re building an extension to your house to get another bedroom. The duration of this project is going to be 20 days, and you’ve allocated $50,000 for it, including all the tools, materials, and furniture.
At the end of day 17, you want to check how the project is doing financially, whether you’ll have to extend the project deadline, and if more funds are needed.
But you’re in for a surprise. You find out that you have spent only $40,000 because you opted to buy some of the furniture at the local thrift stores.
Better yet, you have completed 85% of the work, which means you’re right on schedule.
So, let’s calculate your project’s financial state.
Actual cost (AC) = $40,000
Earned value (EV) = $50,000 x 85% = $42,500
Cost variance (CV) = EV – AC = $42,500 – $40,000 = $2,500
This means that you’re $2,500 under budget.
When the actual cost is below the planned budget, there is a positive cost variance.
3 ways to calculate cost variance
There are 3 different ways to figure out a project’s cost variance:
- Cumulative cost variance,
- Point-in-time (or period-by-period) cost variance, and
- Variance at completion.
Cumulative cost variance
Cumulative cost variance takes into account multiple timeframes. It’s calculated by finding the difference between the cumulative earned value and the cumulative actual cost of a project.
Let’s see how to calculate cost variance in all 3 ways through a simple example.
Imagine you’re working on a project with a budget of $5,000 and have 5 weeks to finish it. Over the course of 3 weeks, you manage to do 65% of the project while spending $3,500.
Here’s a breakdown of the work performance and project costs for each week:
Time period | % of work done | Costs |
---|---|---|
Week 1 | 15% | $800 |
Week 2 | 20% | $1,250 |
Week 3 | 30% | $1,450 |
We can now calculate the cumulative cost variance with the following values:
Actual cost (AC) = $3,500
Earned value (EV) = $5,000 x 65% = $3,250
Cost variance (CV) = EV – AC = $3,250 – $3,500 = -$250
The result shows a negative cost variance, meaning there’s a cost overrun.
Point-in-time cost variance
Point-in-time cost variance measures the cost variance in a single timeframe. It’s also called period-by-period cost variance, and it’s the difference between the earned value and the actual cost of a single project phase or time period — without taking into account previous or future variances.
To calculate these cost variances, we use the same basic formula for CV:
CV = EV – AC
The main difference, however, is in the time period(s) we focus on.
Here’s the EV and AC data for each week:
Time period | EV | AC | CV = EV – AC |
---|---|---|---|
Week 1 | $750 | $800 | -$50 |
Week 2 | $1,000 | $1,250 | -$250 |
Week 3 | $1,500 | $1,450 | $50 |
This example shows us the project missed the budget mark in the first 2 weeks.
There are only 2 weeks left to the deadline, and the budget is running out. So, the project manager must take immediate action and redistribute the remaining budget or find additional funds.
Staying on top of deadlines and budgets is a lot easier when tasks are organized with project management software like Plaky. Here’s how our project can be set up in a single board:
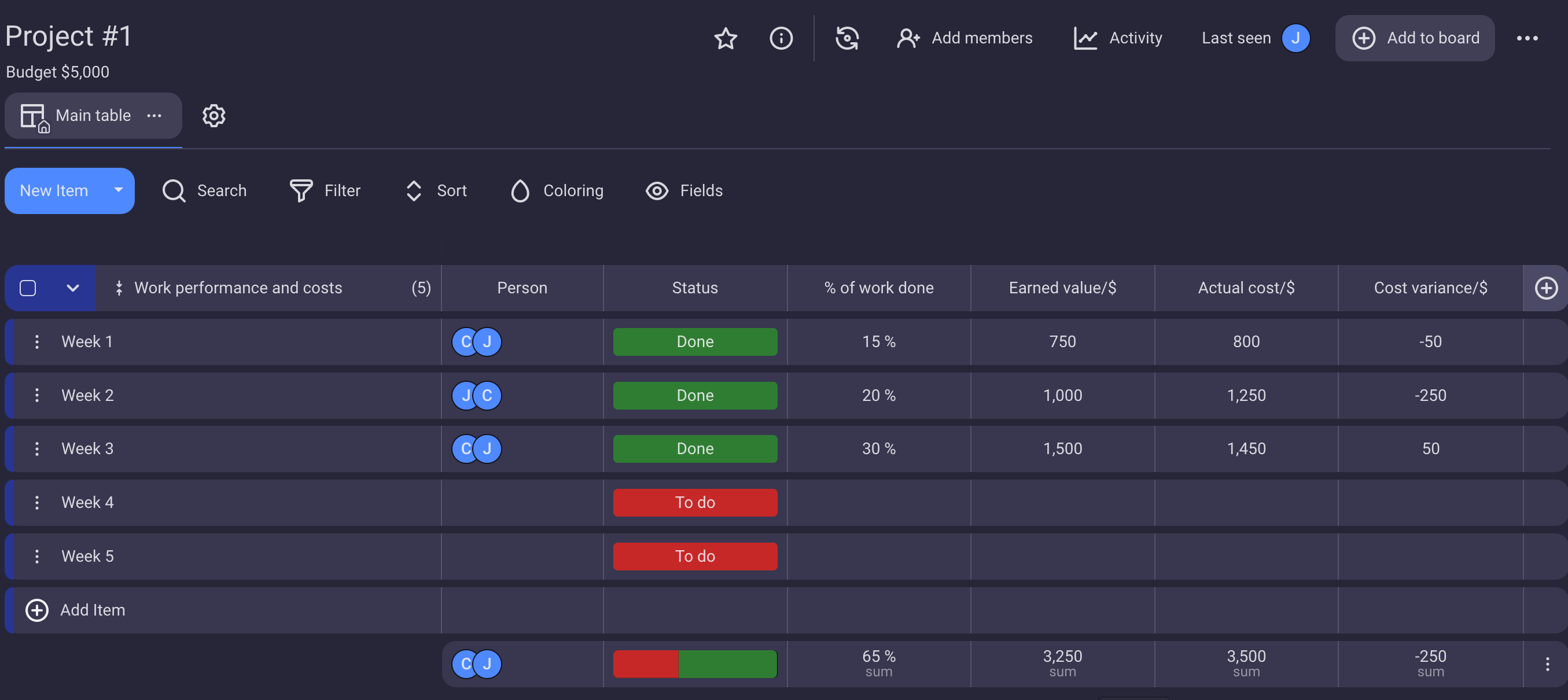
Variance at completion (VAC)
Variance at completion is the difference between BAC (budget at completion) and the most recent EAC (estimate at completion). Its core purpose is to predict if there will be a budget deficit or surplus at the project’s end.
Before we look at the formula for VAC, let’s consider what EAC is and how to calculate it.
EAC represents the predicted cost of the project at its completion, which we can calculate while the project is underway.
EAC can be calculated in 4 different ways, depending on what’s going on with our project:
EAC = AC + bottom-up ETC
EAC = AC + (BAC – EV)
EAC = BAC / CPI
EAC = AC + [(BAC – EV) / (CPI × SPI)]
💡 Plaky Pro Tip
We have a complete guide on how to calculate EAC using these formulas — and how to decide which formula to use. Check it out here:
You may notice that some of the formulas for EAC require CPI.
The cost performance index (CPI) measures the cost efficiency of budgeted resources. It’s calculated as the ratio of earned value to actual cost:
CPI = EV / AC
💡 Plaky Pro Tip
If you want to know more about CPI and how to monitor cost performance, check out this post:
Now that we’ve defined all the elements of variance at completion, we can use this simple formula to calculate it:
VAC = BAC – EAC
Much like CV, VAC can also be positive, zero, or negative. Here’s how to interpret the results:
- Positive VAC — the project will end under budget,
- Zero VAC — the project will use up all of the planned budget,
- Negative VAC — the project will go over the planned budget.
Let’s say there is a project underway whose budget is $500,000. After applying the formula for EAC, you get the result of $505,000.
VAC = BAC – EAC = $500,000 – $505,000 = -$5,000.
So, it’s expected that you will be $5,000 over the planned cost at the end of the project.
Budget at completion (BAC) = $500,000
Estimate at completion (EAC) = $505,000
Variance at completion (VAC) = -$5,000
Types of cost variances in project management
Cost variances can occur in any project, and they are sometimes inevitable or even impossible to prevent.
Here are some of the most common types of cost variances you may run into in project management.
Material cost variance
Staying within the project budget largely depends on your estimates being accurate. You can’t always predict economic conditions, the rates and prices you will have to adhere to, or the exact circumstances linked to their changes.
Contractors may change the prices of tools, materials, and other project resources. Prices may go up due to unforeseen circumstances, and if you don’t have a way of lowering them, you might end up with a negative cost variance.
Whatever the reasons behind the changes may be, they will inevitably prevent you from accurately reporting on the project’s progress. So, if you notice that the changes are constant, and not a one-time thing, make sure to reevaluate your budget and project scope.
💡 Plaky Pro Tip
Do you know what scope creep is and how it can affect your projects? Learn all about it in this post:
Labor cost variance
If the project’s requirements change, the scope may also suffer some modifications. These changes may include adding or eliminating certain project activities.
If it takes more time to complete the project, the labor cost goes up, leading to negative labor cost variance. The same happens if the wages go up.
Alternatively, if some activities prove to be unnecessary, the costs will be lower than predicted, and the project will end up with a positive cost variance.
Variable overhead variance
Variable overhead costs vary depending on productivity. It’s up to project managers to make a reliable estimate of potential manufacturing, shipping, or marketing costs.
A bad estimate could signify that a cost variance is just around the corner. So, it’s important to monitor and manage the estimates throughout the project’s life cycle.
Fixed overhead variance
Fixed expenses don’t vary regardless of productivity. Expenses such as rent, wages of regular employees, and taxes are all long-term costs that don’t change quickly or often.
Unless there are significant sudden changes, these costs shouldn’t affect a project’s cost variance.
How to keep your projects on the right track
Project managers are in charge of delivering high-quality project deliverables while handling the 3 project constraints: scope, time, and cost.
Keeping a project within budget can be a challenge due to the many unforeseeable circumstances that affect the project’s financial performance.
Here are 5 tips to help you avoid negative cost variances and keep your project budget and expenses in check:
- Set realistic and accurate goals and estimates,
- Plan out your costs with WBS,
- Keep track of your project’s KPIs,
- Investigate cost variances regularly, and
- Continue to forecast throughout the project’s life cycle.
Let’s discuss these tips in more detail.
Set realistic and accurate goals and estimates
Setting realistic project goals and estimates can be achieved by taking historical data into account. It’s common for project managers to look at previous similar projects and create a roadmap that reflects past experiences.
The budget, scope, and project timeline must be accurate and feasible. Otherwise, you’ll fall into the trap of overpromising and under-delivering.
The estimation process can and should include the team and project stakeholders. They can give valuable feedback that lets project managers make a more detailed cost breakdown and potentially prevent both negative and overly positive cost variances that give wrong budget assumptions.
💡 Plaky Pro Tip
Learning from your past experiences is vital for becoming a better project manager and leading successful projects. The post-implementation project review and lessons learned are 2 tools that can help you on that mission. Check out our guides on both:
Use a WBS for cost planning
A work breakdown structure (WBS) is a catalog of every task you need to do to complete a project.
A WBS can also serve as a guide for a cost breakdown as it includes 100% of the project-related work.
When making a WBS, strive to be as detailed as possible. That way, you will lower the chance of omitting an important expense that could lead to a cost variance later on.
An expert we reached out to, Carla Jenkins, a PMP-certified Senior Project Manager at Phenomena Corporation, suggests going the extra mile when preparing your budget and outlining the potential costs:
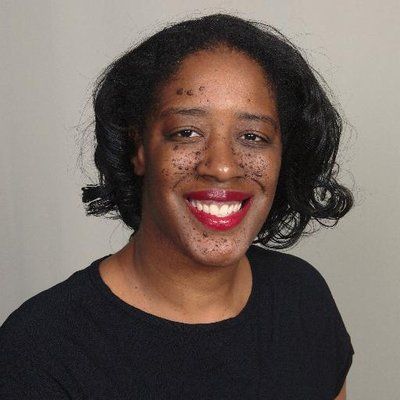
“I draft 3 different budgets using the 3-point method based on most likely, best-case, and worst-case scenarios. Having these 3 different budget baselines helps me gauge if I need to ask for help securing more people and resources.”
Track project KPIs
Some of the most useful project management KPIs you can track to keep your budget in check include:
- Earned value (EV),
- Actual cost (AC),
- Cost variance (CV), and
- Cost performance index (CPI).
You can always choose to track more than these 4 KPIs.
For example, planned hours vs. time spent is a rather handy KPI, as tracking the time you spend on each project task and comparing it to your estimates will show you the accuracy of your schedule.
While monitoring KPIs, it’s also essential to review them regularly with your project team and stakeholders. Everyone should have a clear idea of the project’s progress and the roadblocks it faces.
Investigate cost variances regularly
Cost variances can be a result of various issues and changing circumstances. Their effect on the whole project can be monumental, so it’s necessary to keep tabs on them regularly.
You can investigate each type of cost separately to determine where and why the variance has occurred.
For instance, if you’re consistently missing the mark in terms of labor costs, you could examine why the variance keeps happening and use corrective measures to reduce it.
A major part of project cost control includes establishing variance control thresholds. These are set amounts of variation that don’t require any corrective action.
Corrective action should always involve the proper identification of the causes and their consistency.
Forecast continually
Our final tip is to continue forecasting your project’s cost performance until it is completed.
It’s important to watch the budget closely and keep forecasting frequently due to the impact project changes have on costs.
Consistent re-forecasting allows you to stay on top of all costs-related matters within the project’s life cycle. You’ll also be better at gauging the project’s progress.
The expert we reached out to, Carla Jenkins, says that she re-forecasts on a routine basis.
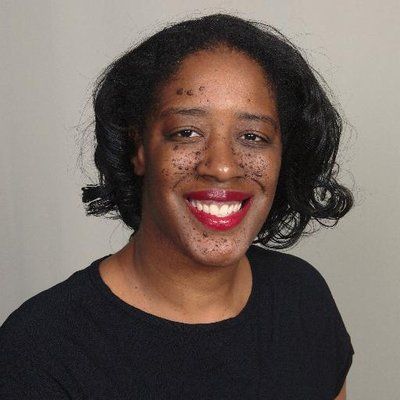
“At the end of my week, I re-forecast my budget. I do it every week so that I do not miss any trends or developments.”
Re-forecasting her budget on a weekly basis allows Jenkins to be proactive about cost control:
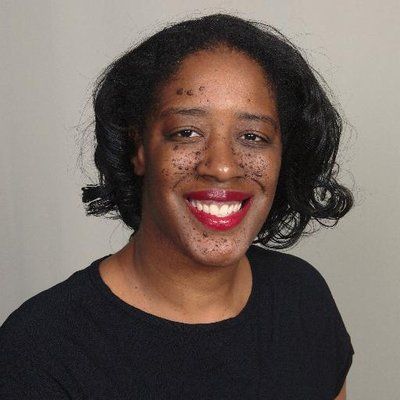
“I also want to see if we’re at least on budget or under budget. If we’re over budget, let’s see where we can cut costs by either streamlining resources or seeing where we can cut.”
That said, there’s no point in forecasting if you don’t know what to do about the changing circumstances of your project’s cost performance. So, make sure you have a plan B, C, and even D in place in case your project costs become more of a headache.
You need contingency plans to keep the project on the right track even if conditions such as costs change.
That way, you can balance out your project’s cost performance and minimize any potential cost variances that may occur.
📖 To go beyond cost variance and even the EVM terminology, dive into our Project Management Glossary of Terms.
Track all project costs with Plaky
Specialized organizational software such as Plaky can help a great deal with managing costs and keeping the relevant KPIs of your projects in one place for effortless tracking and comparison.
Plaky can help you manage your projects successfully by:
- Offering plenty of project management templates to set up projects quickly,
- Improving team collaboration with task-specific comment threads,
- Integrating with Clockify to facilitate project time management,
- Letting you choose between Table, Kanban, and Gantt views,
- Allowing you to share files with the team, and
- Automating your calculations.
You can also create custom fields and easily adapt the board to your needs, no matter how many different types of projects you’re managing. In fact, Plaky is the only software you need for tracking project progress, cost control, and team collaboration — all in one place.
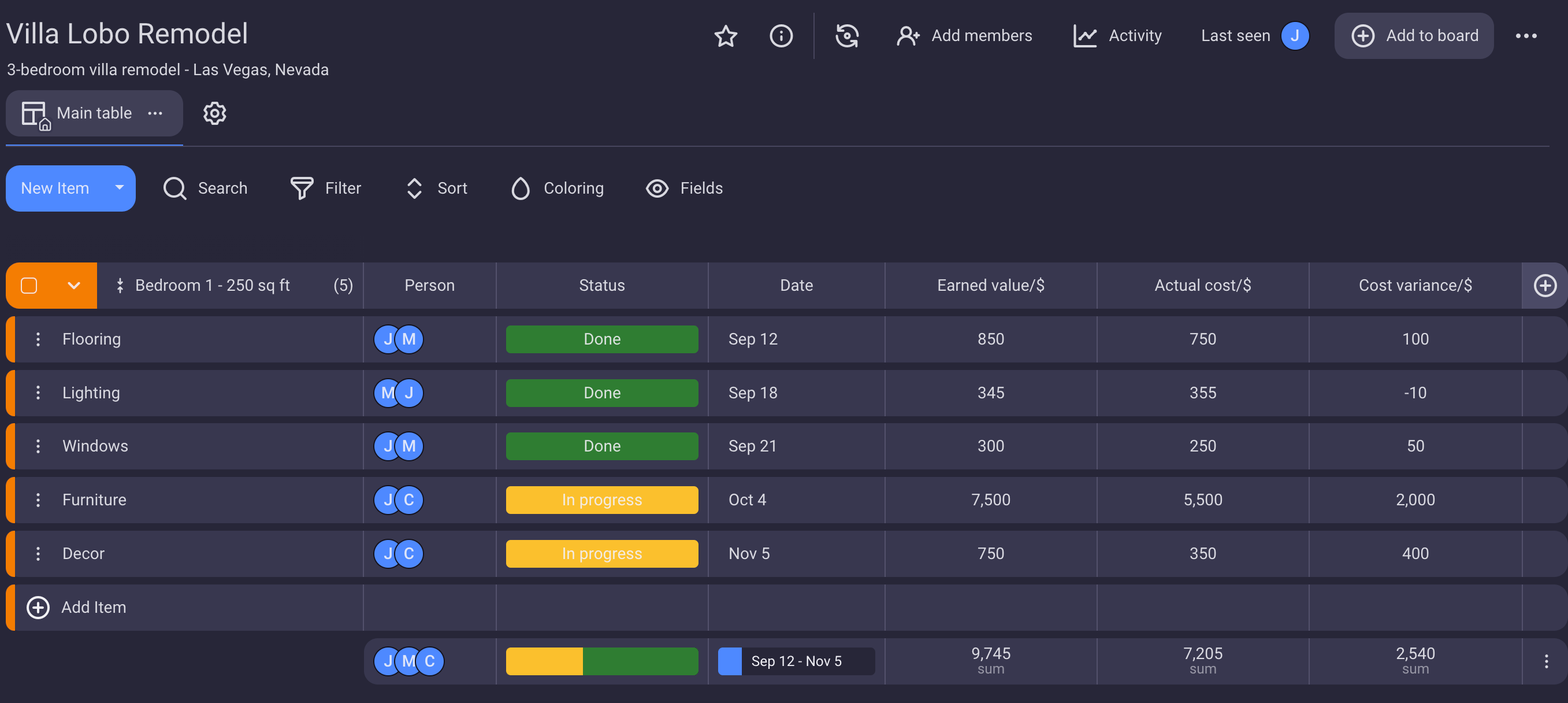
Try all of Plaky’s features and ensure proper project cost control by creating a free account and enjoying a 14-day trial!