A lot of managers use what I like to refer to as “Schrödinger’s capacity planning.”
In other words, they make plans, close deals, and commit to projects without really knowing the capacity of the resources at their disposal.
Maybe they have the capacity to tackle a new project, maybe they don’t — they’ll find out once said project starts.
The problem? This is exactly how you get awkward situations where:
- People who are already working at full throttle get assigned to yet another project, or
- A client gets promised a product that is impossible to deliver on time.
Want to avoid these (highly and easily avoidable) situations? Focus on capacity planning.

Table of Contents
What is capacity planning anyway?
Capacity planning is the process of matching your capacity — this includes all project resources you have available, like products, tools, and human resources — to the demand placed on it by upcoming projects.
The goal of capacity planning is to avoid situations where you have too few or too many resources compared to the actual demand.
But why is capacity planning important?
Essentially, capacity planning improves organizational efficiency by providing answers to these 2 questions:
- Do we have the capacity to complete current projects?
- Do we have the capacity to take on extra projects?
To illustrate, imagine that you’ve got 2 pilots and 10 planes.
Obviously, you can’t schedule 10 concurrent flights — there simply aren’t enough human resources to pull this off.
On the other hand, if you’ve got 10 pilots and only 2 planes, you can still only schedule 2 concurrent flights because you don’t have enough tools.
So, you’re either:
- Meeting demand and wasting money on excess capacity, or
- Failing to meet demand.
And trust me — neither option is good.
If you’re already meeting demand, then you’re wasting a lot of money on idle resources, and if you’re not, you’re limiting your profitability by investing in the wrong resources.
What both situations have in common is wasted money.
The 3 main pros of capacity planning
The 3 main benefits of capacity planning are:
- Reduced costs — matching your capacity with actual demand helps plug up resource leakages. For example, buying and storing twice the amount of raw materials you actually need doesn’t only freeze up a portion of your liquid assets — it also runs additional warehousing costs. Proper capacity planning reduces costs by eliminating these wasteful leaks.
- Increased profitability — in addition to reducing costs by avoiding wasteful spending, capacity planning also increases profitability by enabling you to respond to increased demand. By accurately projecting an increase in demand, you give yourself time to increase your capacity appropriately and seize the opportunity.
- Reduced bottlenecks — by analyzing your current capacity, you’re able to spot workflow bottlenecks and inefficiencies and address them. This could happen at any resource level — it could be a particular employee who is overloaded with work because no one shares their skillset or a piece of equipment that needs to be in two places at once.
The 1 major con of capacity planning
However, for all the good capacity planning does, it has 1 glaring downside:
Capacity planning is difficult to do accurately.
Its results are only as good as the data you put in. In other words, if your demand projects are wrong or your capacity assessment inaccurate, then you won’t enjoy any of the previously mentioned benefits.
This may sound like it should go without saying, but it’s important to note because assessing your current capacity accurately isn’t something you’re supposed to do only once.
Good capacity management demands frequent reassessment of actual capacity, which is constantly changing across several dimensions, like the 3 major types of capacity and their subtypes.
So, while it can pay dividends, capacity planning is also something that requires consistent effort.
Types of capacity planning
The 3 main types of resources to keep in mind while working on a capacity planning strategy are:
- Workforce capacity,
- Product capacity, and
- Tool capacity.
Workforce capacity planning
Workforce capacity, also known as human resource/capital capacity, compares how many people a project requires versus how many people you’ve got available.
It’s often calculated in working hours. So, a project team of 5 people each working 40 hours a week would have a weekly capacity of 200 hours.
Now, the issue is — if working on their current projects takes up 180 hours a week, then taking up a project that would demand an extra 80 cumulative working hours a week would exceed your team’s capacity supply.
This would either result in unhappy workers — and burnout, over a longer period — or an unhappy client.
Of course, this kind of workload management isn’t the only way to approach workforce capacity planning.
Workforce capacity planning also takes into consideration the skills and roles of the employees. In fact, a good manager will keep the strengths and weaknesses of their team members in mind while allocating tasks to make the most efficient use of available workforce capacity.
If your workforce capacity plan shows that you don’t have enough people to complete upcoming tasks and projects, this can serve as a major red flag to start hiring before insufficient capacity becomes a problem.
On the other hand, if your workforce capacity exceeds demand, consider:
- Reorganizing your teams,
- Taking on more projects, or
- Downsizing.
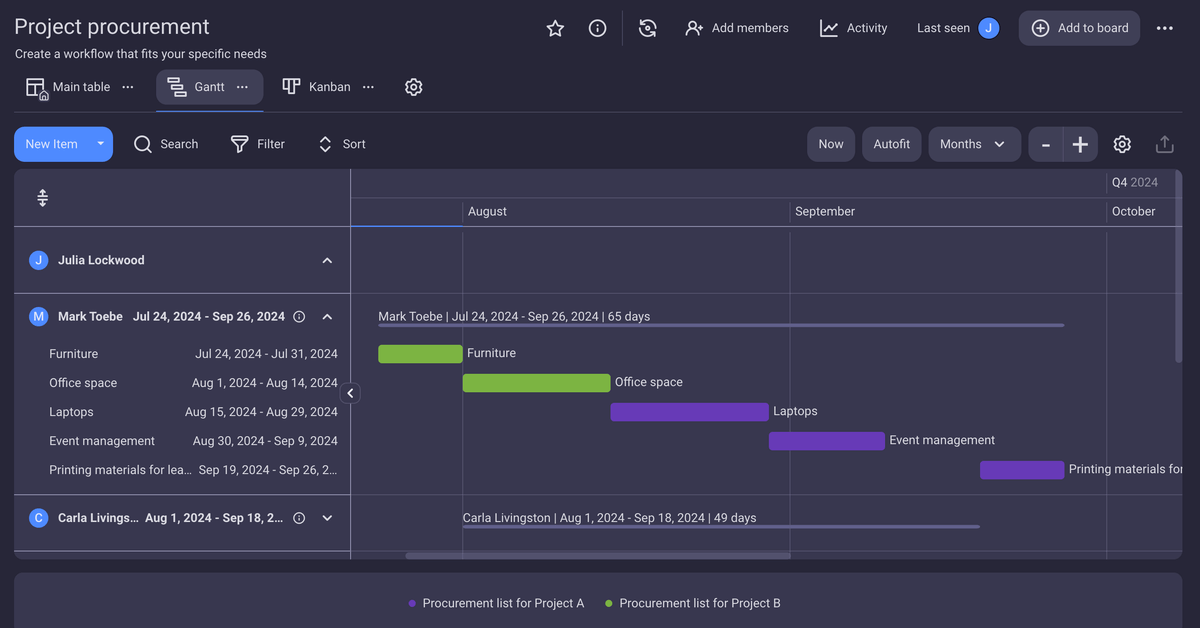
Product capacity planning
Product capacity planning refers to the acquisition and management of resources needed to make the product you’re selling.
One example of this would be the raw materials you’d need to manufacture your product. Since supply chains can run long, quickly getting your hands on more materials to respond to a spike in demand can be tricky — thus the need for capacity planning.
Product capacity, especially when referring to raw materials, can often be the biggest bottleneck when it comes to your inability to meet demand. Plus, long supply chains usually make it difficult to quickly respond to demand spikes.
Meanwhile, excess capacity is undesirable as it costs you in storage space/expenses and limits your liquidity. That’s why product capacity planning is crucial in industries like manufacturing.
However, product capacity can also play a crucial role in the service industry, depending on the service you’re providing. For example, accounting firms don’t have to worry about product capacity, but restaurants certainly do, since they’re also responsible for manufacturing the dishes that they serve.
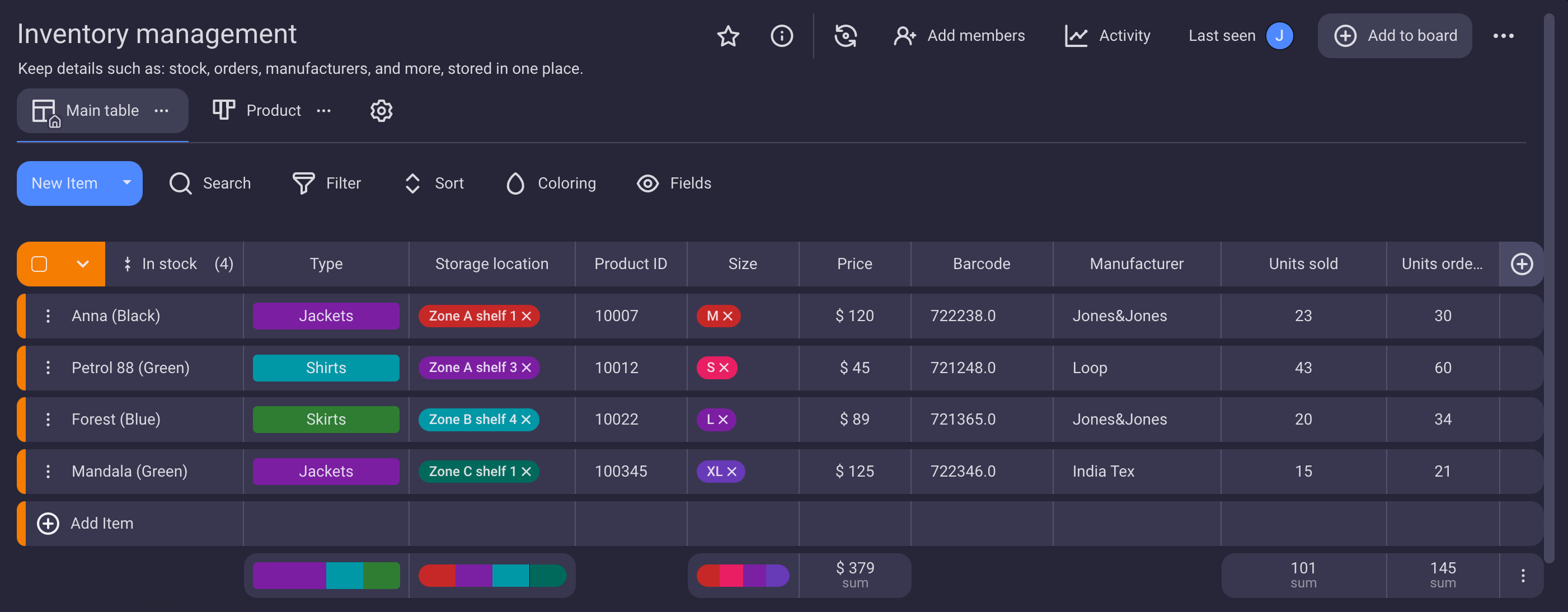
Tool capacity planning
Tool capacity planning is used to figure out whether your teams are adequately equipped to handle upcoming projects and tasks.
This obviously includes all the equipment needed for a project, like computers, vehicles, specialized equipment for manufacturing, etc. But it also includes digital tools.
For example, managers can utilize digital tools like Plaky to keep track of human resource capacity and availability, as well as task management and other project management requirements. This way, they can:
- Avoid task duplication,
- Keep track of actual resource cost per task,
- Have clear insight into each team member’s role in the project workflow,
- Spot resource bottlenecks, and
- Plan ahead accordingly.

3 capacity planning strategies you can use
As mentioned, capacity planning is the act of matching your resource capacity to the projected demand for it. Depending on how you go about projecting demand, we can talk about 3 types of capacity planning strategies:
- Lead,
- Lag, and
- Match.
Lead strategy
The lead strategy for capacity planning entails projecting demand and then structuring your available resources around meeting that demand.
The biggest benefit of the lead strategy is that it allows you to respond to sudden increases in demand.
However, since it doesn’t use actual, current demand as input for its equation — but rather some future, potential demand — it runs the risk of overspending on excess capacity that won’t be put to any use.
For example, imagine you expand your servers and hire a new network administrator to maintain them, expecting your service to receive an influx of new users.
If this does happen, congratulations — the lead strategy paid off!
But if, for whatever reason, it doesn’t happen, you’ll be stuck with bigger servers than you need.
Sure, these servers may prove useful at some point in the future, but in the medium-to-short term, they’re money down the drain.
Lag strategy
The lag strategy for capacity planning is the opposite of the lead strategy — it responds to actual demand.
By limiting your capacity planning to actual demand, you avoid overspending and keeping resources idle. So, you could call this a lean strategy too, since it seeks to eliminate waste in the form of overspending and idle resources.
However, the downside of this strategy is that it’s the opposite of agile — it’s slow to respond to big shifts in demand.
In terms of selling products, this would refer to stockouts. Clients who decide they want more of your product will be disappointed — and maybe even take their business elsewhere — as your resource capacity won’t be able to handle this.
To illustrate, let’s use the same server example from before.
Imagine your service has suddenly received a huge influx of new users that your server infrastructure cannot support.
But, by the time you expand your servers and hire a new network administrator, the moment to capitalize on the increase in demand may well be gone — with users having gone to your competitors.
Losing out on potential customers is already bad enough. In this example, though, your profitability will also be hit by the untimely investment in new servers and a network admin.
Match strategy
The match strategy to capacity planning takes the best of both lead and lag planning.
This is done by monitoring actual demand, but keeping the capacity a bit above it. Doing this gives you some breathing room to respond to unexpected increases in demand, without keeping too much excess capacity.
The match strategy is, by far, the most involved strategy, as it requires frequent demand projecting and capacity readjusting. However, it rewards this effort by reducing overspending and idling while still keeping room to respond to extra demand.
This strategy is also great if you’ve got products or services that experience seasonal spikes in demand. In these cases, you should expand your capacity to account for these expected shifts.
How to increase efficiency with capacity planning in 5 steps
So, now that you know all there is to know about capacity planning, how do you actually utilize it?
It’s pretty simple — you just need to follow these 5 steps:
- Project demand,
- Define the needed capacity,
- Measure the current capacity,
- Calculate the capacity gap, and
- Align the capacity with the projected demand.
Step #1: Project demand
Step one entails projecting future demand — but how you do this is up to you and your strategy.
Lag strategies take for granted that demand won’t change much, whereas lead strategies assume a shift in demand is incoming.
You can also use different strategies at different times. For example, it’s customary in many markets for demand to skyrocket during holidays, only for levels to then revert back to normal afterward.
In any case, you need to leave this step with a concrete idea of the demand you’ll expect.
Step #2: Define the needed capacity
Once you know what demand you’re preparing for, you need to calculate the needed capacity:
- How many people will this undertaking require?
- What skills?
- Which and how many tools?
- What products?
The projected demand and the needed capacity should function like an equation — equally weighed on both sides.
Step #3: Measure the current capacity
Now, take stock of your current capacity:
- How many people do you have on your team?
- What are their skills?
- How many tools do you have?
- What raw materials?
This step will help you identify bottlenecks in your current processes.
A bottleneck could occur across any level of resources — it could be a piece of equipment, a key employee whose skills are needed across multiple projects, or anything else.
Whatever the case, your project workflow will suffer from delayed tasks or missed deadlines.
By identifying these bottlenecks, you can work to prevent this. The solution could be storing more raw materials, hiring an employee with skills that are sorely lacking, or buying more tools — but you have to diagnose the problem first.
Step #4: Calculate the capacity gap
Now, measure the discrepancy between the needed capacity and your actual current capacity. This will let you know where you stand with regard to each resource and help you figure out:
- What you need more of, and
- What you have a surplus of.
Step #5: Align the capacity with the projected demand
Finally, take the steps needed to match your capacity with the projected demand.
In other words, work to close the capacity gap you’ve identified in the previous step to 0.
FAQ
Capacity planning vs resource planning
Capacity planning takes a bird’s eye view of a company’s (or team’s) overall capacity to strategically plan ahead and match supply to future demand.
Resource planning, on the other hand, zooms in on a particular resource required for a project and its current availability.
Plaky Pro Tip
Learn about managing individual resources in our resource allocation guide:
Capacity planning vs capacity requirements planning
Capacity planning and capacity requirements planning (CRP) are the same thing.
Capacity planning vs capacity management
Capacity planning is the process of defining current and future capacity and demand.
Capacity management is the process of monitoring, analyzing, and optimizing organizational (or team) capacity.
Optimize your capacity planning with Plaky
Without capacity planning, you’re essentially gambling on whether or not you have the capacity to tackle incoming projects.
And sure, sometimes you win when you gamble, but you also often lose — so approaching projects with this kind of attitude is just irresponsible.
That said, capacity planning is only as good as the input that it uses. If inaccurate data goes in, inaccurate data comes out.
So, to ensure that you’re using accurate data for capacity planning, use Plaky.
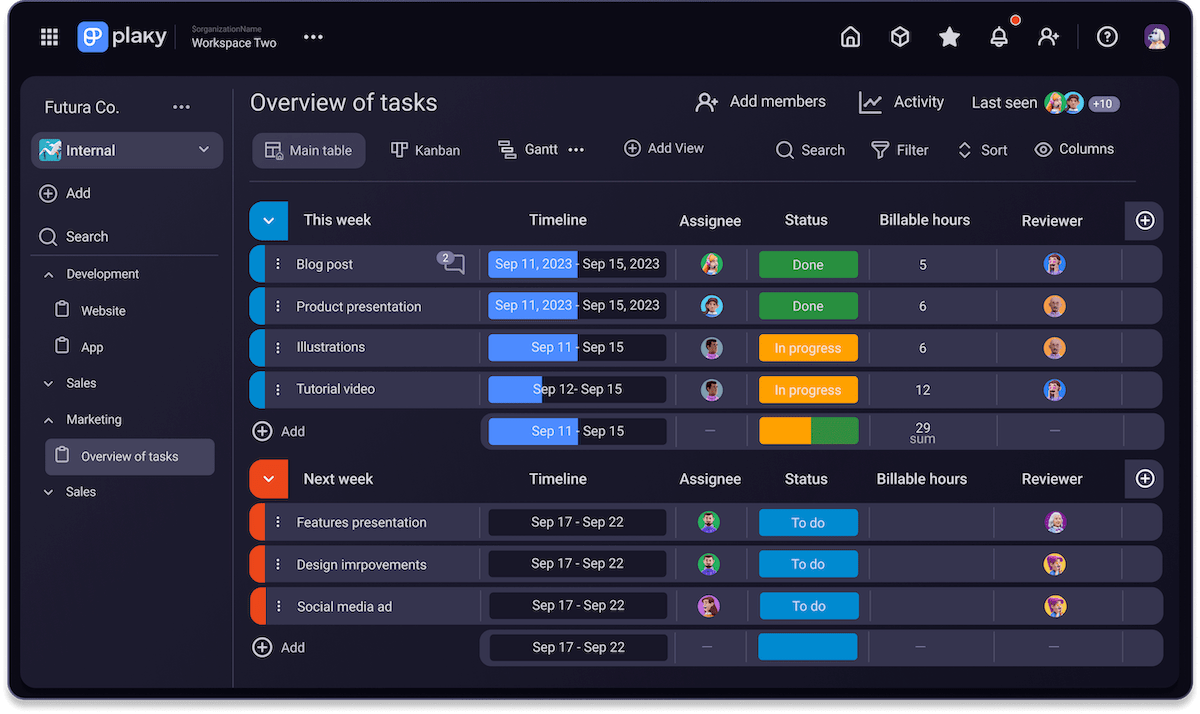
Track all relevant resources to determine your capacity with Plaky’s customizable project and task management features:
- Assignees and dates for workforce capacity,
- Custom tags for product capacity, and
- Custom tags and statuses for tool capacity.
Transform your capacity planning efforts with Plaky. Sign up for a free Plaky account now and try out all premium features for 2 whole weeks.